Project Category: Chemical
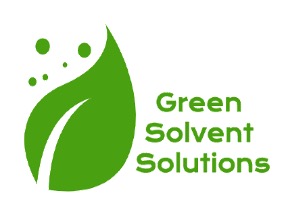
Big thanks to our judges, family, & friends that came to chat with us!
Zoom meetings are not closed!
About Our Project
The accumulation of carbon dioxide, the most significant human-produced greenhouse gas (GHG), in the atmosphere has continued to climb, year after year. The atmospheric concentration of CO2 has increased from 280 ppm in the pre-industrial age to approximately 410 ppm in 2019 and is expected to increase above 500 ppm by the end of this century. To remediate the impact on the climate, direct air capture (DAC) has been proposed as a truly negative CO2 emissions technology. Green Solvent Solutions has examined the design and financial viability of a plant in Quebec to produce 1000 tons of methanol a day using the novel technologies DAC and carbon dioxide electrolysis. The project focuses on the utilization of hydroelectric energy to produce syngas which is used to generate methanol. The power-to-methanol pathway presents the opportunity to divert carbon dioxide from the air while producing a valuable chemical feedstock.
Block Flow Diagram
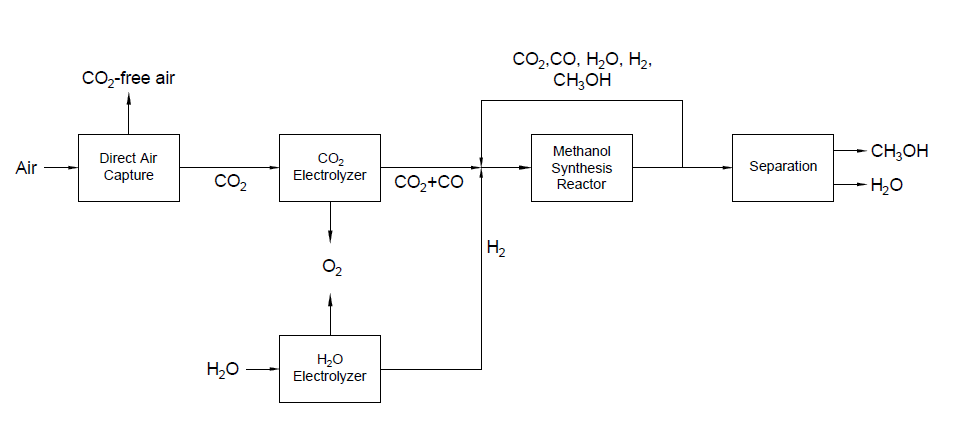
Plant Layout & Maps
Downloads
Details About Our Design
HOW OUR DESIGN ADDRESSES PRACTICAL ISSUES
One of the main barriers to producing methanol using DAC and CO2 electrolysis is that for a power-to-methanol pathway to be a viable green process, electricity needs to be provided by a low carbon source. These electricity sources often have variable capacities and cannot be relied on to deliver continuous power. GSS considered various locations and energy sources across Canada and determined that hydroelectric power in Quebec was the best choice. Hydropower has very low emissions (1.2gCO2/kWh) and is not weather-dependent like solar or wind power. In addition, HydroQuebec offers low-cost power ($0.0346/kWh) and has a high capacity (40 000 MW) to deliver continuous power.
WHAT MAKES OUR DESIGN INNOVATIVE
Traditional methanol production relies on the production of syngas from methane or coal. GSS’s design uses the power-to-methanol pathway to generate syngas using electrolysis powered by renewable energy to advance the ambitious goal of reducing the impact on the climate.
The proposed design sequesters CO2 from air using the chemical binding adsorption method with potassium hydroxide (KOH) as the sorbent. The concentrated CO2 stream is converted to CO in a solid oxide electrolysis cell (SOEC). The hydrogen required is provided by the electrolysis of water in a proton exchange membrane (PEM) electrolysis cell. These gases are fed into a reactor to produce methanol using a copper/zinc oxide/alumina catalyst. This methanol can then be used in a variety of industrial processes.
WHAT MAKES OUR DESIGN SOLUTION EFFECTIVE
One way of presenting how effective our design solution is to see how successful DAC is with removing non-point, historical emissions from the atmosphere despite the extremely low concentrations of CO2. Using the KOH sorbent, the DAC unit can successfully capture 75% of the CO2 from air stream entering system.
The combined technology in the proposed GSS designed facility provides a green alternative to conventional methanol production making the overall process an effective solution to removing CO2 from air while producing a viable revenue stream.
HOW WE VALIDATED OUR DESIGN SOLUTION
Detail design was conducted only for the reactor and separation unit.
Our proposed design solution was validated using hand calculations, process simulation, and additional programs such as KG Towers and MATLAB for Distillation Column and Methanol Reactor respectively.
Methanol Reactor
A plug flow reactor was modeled for methanol synthesis. The kinetics used were from papers by Graaf et al. 1986-1988 and were programmed into VMG Symmetry using the Advanced Peng Robinson property package. Using literature and plant data from Samimi et al. 2017 and Muflih et al. 2020 a comparison to output flows was done, shown in the tables below.
The fugacity coefficients used in the advanced kinetics of VMG Symmetry were programmed and calculated in MATLAB to confirm the kinetic model comparing to Chang et al. (1986) as shown in the figures below.
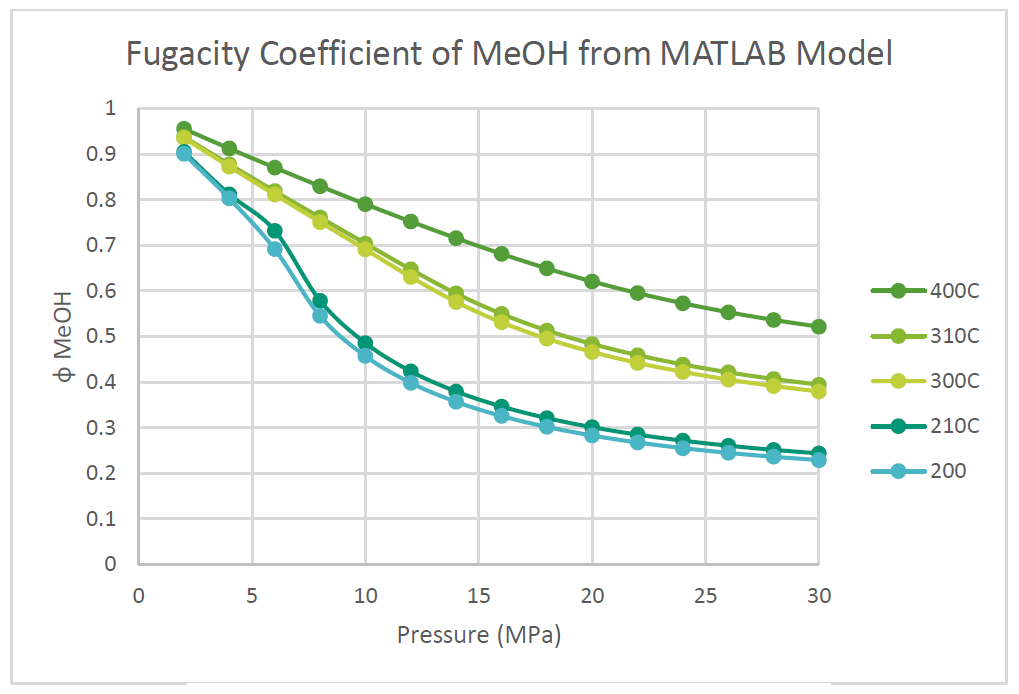
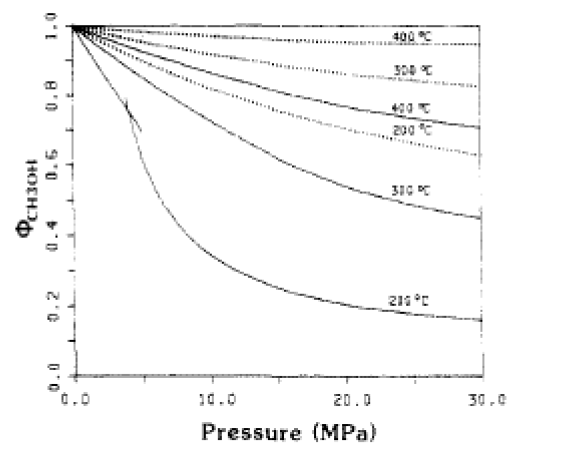
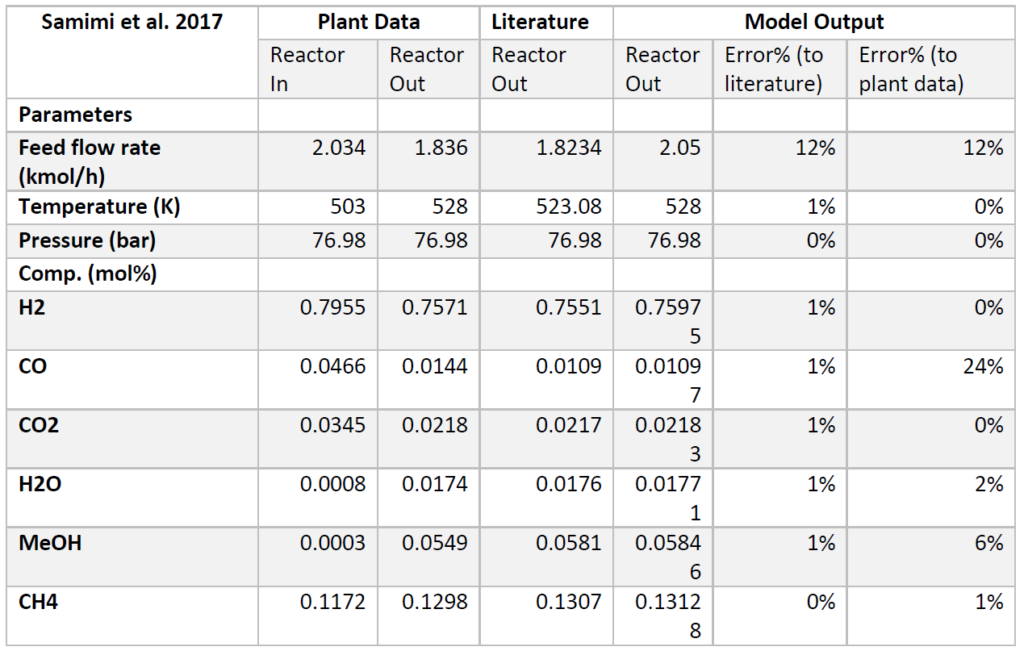
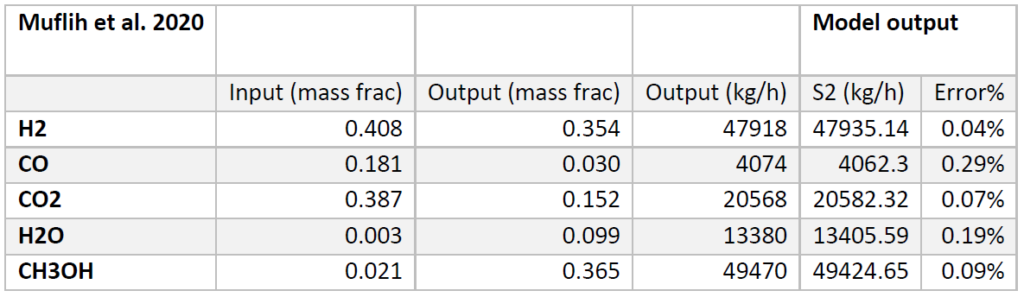
Distillation Column
A partial condenser distillation column for separating and purifying methanol was initially simulated in VMG Symmetry using the Advanced Peng Robinson property package. After the detailed design of the column, the ideal number of stages was found to be 32 with a reflux ratio of 0.98. This distillation column produces a methanol purity of 99.8wt%. VMG Symmetry Tower Sizing option and KG-Towers Software were used as independent methods to validate the column design.
Methods | Diameter (ft) |
VMG Symmetry | 11.5 |
KG-Tower | 11.2 |
Results calculated from the VMG Symmetry are very close to the results from KG-Tower. The diameter of the distillation column is essentially chosen to be 12ft. The distillation column is chosen to be tray type due to the easy control and the tray type was selected to be sieve as it is suitable for low to moderate pressure drop.
Advanced Peng Robinson property package was validated comparing isobaric vapor-liquid equilibrium (VLE) data of methanol and water from VMG Symmetry and 1993 experimental binary data.
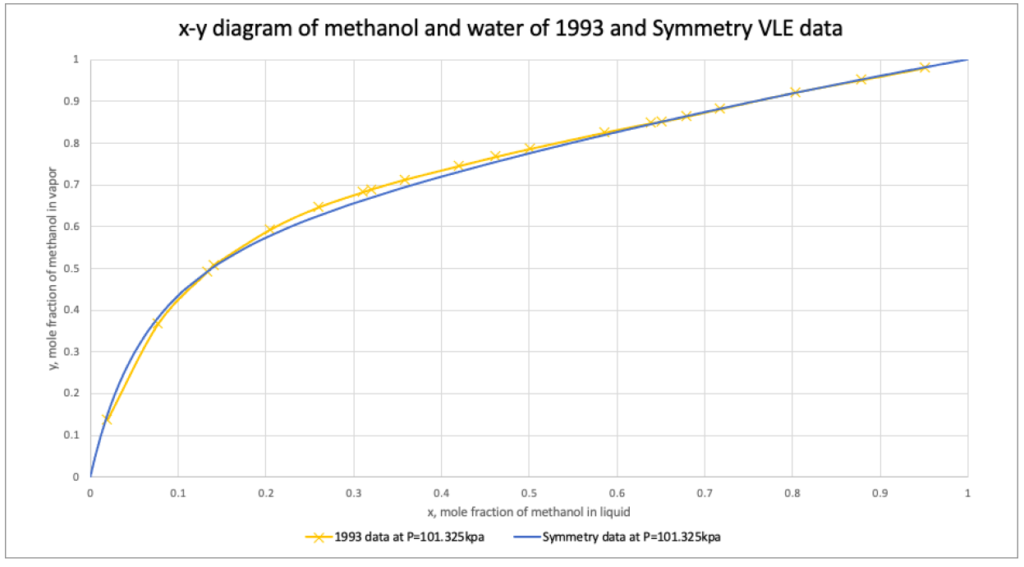
FEASIBILITY OF OUR DESIGN SOLUTION
The cradle-to-gate life cycle analysis for GSS’s process, when powered by hydroelectricity, concluded that for every ton of methanol produced –0.81 tons of CO2 will be removed from the atmosphere. The amount of CO2 emitted when methanol is produced by coal is 3 tCO2/tMeOH and 0.67 tCO2/tMeOH for methanol from steam methane reforming.
The technologies for SOEC and PEM are rapidly improving and in the next 20 years it is expected that the cost for PEM and SOEC will decrease by 50% and 80%, respectively. This will improve the Net Present Value (NPV) by 27%.
From an economics perspective, our NPV is -$10.1B which suggests the process isn’t profitable. This is mainly due to the high initial investment of the DAC unit, PEM, and SOEC equipment and the high costs associated with operating the process. However, with further improvement of these technologies decreasing these costs and government and other industry support such as grants, tax credits, and public procurement due to the process being net-negative, the process can be more economically feasible.
GSS Team Members
Inaara Mawji
Lead Economics, Process Design
Schulich School of Engineering
University of Calgary
2500 University Drive NW Calgary, AB, T2N 1N4
email:Inaara.Mawji@ucalgary.ca
Leslie Kingston
Project Manager
Schulich School of Engineering
University of Calgary
2500 University Drive NW Calgary, AB, T2N 1N4
email:Leslie.Kingston@ucalgary.ca
Shelley Newby
Lead Reactor, Process Design
Schulich School of Engineering
University of Calgary
2500 University Drive NW Calgary, AB, T2N 1N4
email:Shelley.Newby1@ucalgary.ca
Sabheen Uddin
Lead Separation, Process Design
Schulich School of Engineering
University of Calgary
2500 University Drive NW Calgary, AB, T2N 1N4
email:Sabheen.Uddin1@ucalgary.ca
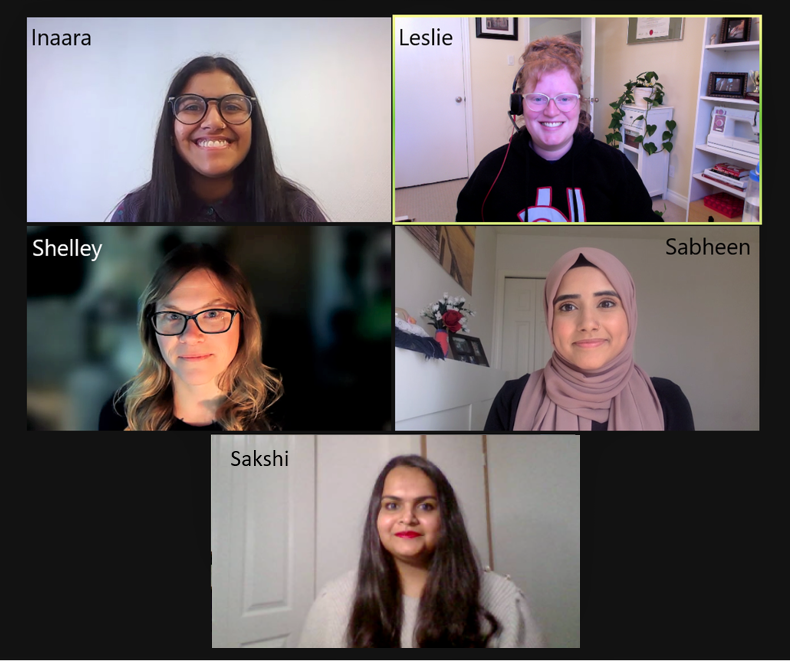
Sakshi Shrivastava
Lead Safety, Process Design
Schulich School of Engineering
University of Calgary
2500 University Drive NW Calgary, AB, T2N 1N4
email:SShrivas@ucalgary.ca
Any questions?
Please Join Us!
Partners & Mentors
We want to thank the many people who helped us with this project, specifically our supervisor for the project Dr. Md Golam Kibria, our chemical process design professor Dr. Hector De la Hoz Siegler who provided great insights and lectures, and the many teaching assistants whom we reached out to and received invaluable guidance from.