Project Category: Chemical
About our project
Rare earth elements are primarily used in catalyst production and strong magnets (like those used in computer hard drives and other electronics). Currently most electronic recycling plants do not handle rare earth recycling due to the difficult nature of separating rare earths; in fact, there is currently only one plant in North America that is equipping itself to handle rare earths. Instead, the rare earth elements are produced from large scale mining operations primarily located in China. In these mining operations, large swaths of land are stripped down to achieve marginal amounts of the rare earths. This process seeks to take advantage of the exponential growth in electronic waste to create a process which is more environmentally friendly than conventional mining operations currently used.
The process is aimed to provide a recycling process scaled to fit Alberta. The process is capable of fitting in a small warehouse and will provide an economically and environmentally sustainable alternative to traditional mining methods. To make the process economically viable, recovery of gold is a required secondary objective of this process.
Meet our team members
William Anderson
Stirling Cenaiko
Alyssa Sommerville
Aaron Milos
Richard Watt
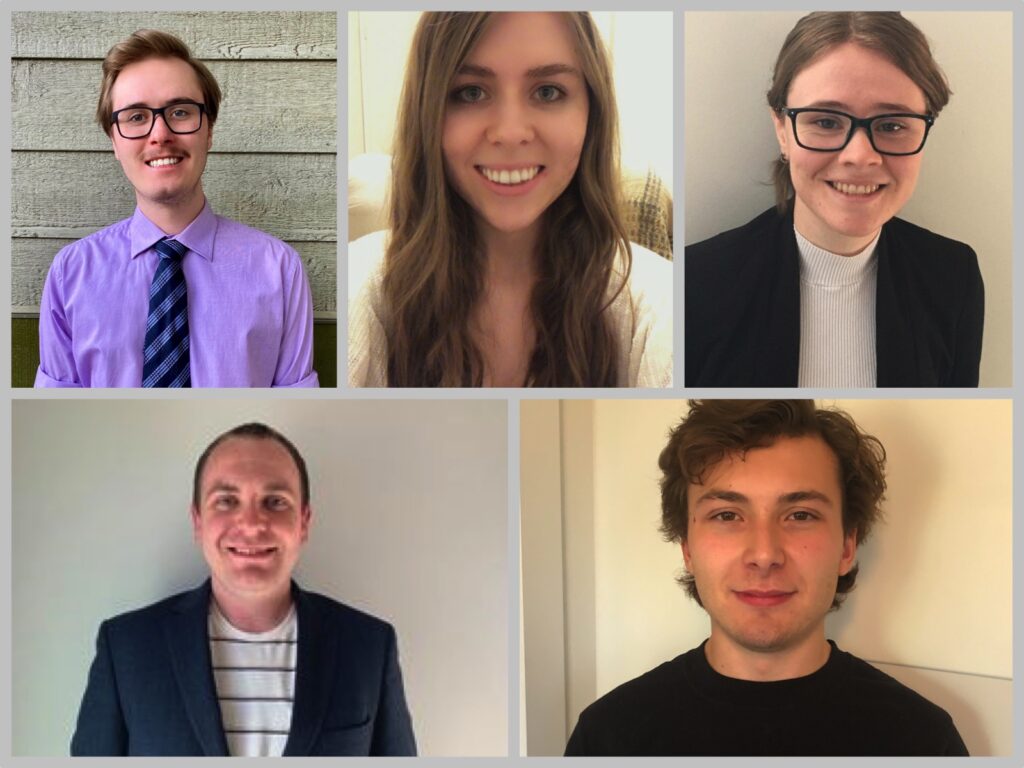
Details about our design
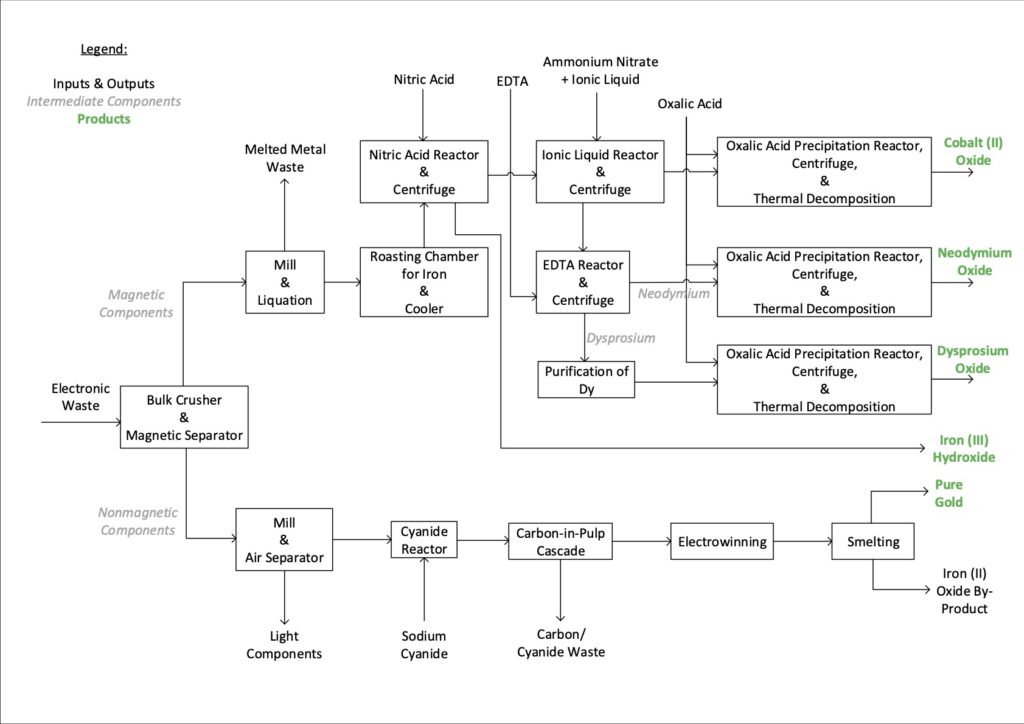
HOW OUR DESIGN ADDRESSES PRACTICAL ISSUES
While it is not at all unusual to find gold or iron ores containing >98% of the metal, rare earth elements (REE) are only found in trace amounts – with ores containing a mere 2-15% of a single element, depending on the region [1]. Largely due to these exceedingly low concentrations, the recovery of REEs from mineral ores is often as little as 50%, requires 20-160 tonnes of rock, and ~1,700 kWh to extract 1 tonne of REEs [1]. Over 100,000 tonnes of REEs are mined each year in this way. New methods to recycle and recover REEs from electronic waste (e-waste) can decrease waste in landfills and build a more sustainable foundation for the growing tech industry.

Rare earth mining operation in California, USA
Image from: https://www.npr.org/2011/01/31/133372641/california-challenges-china-in-rare-earths-mining
WHAT MAKES OUR DESIGN INNOVATIVE
The REE-cycle team has developed a process which can recover REEs from hard disk drives (HDDs), with the potential to modify the process to recycle other components of devices in the future. The process is able to recover ~80% of the neodymium (Nd) and dysprosium (Dy), and over 90% of the iron (Fe), gold (Au), and cobalt (Co) as separate elements, based on results from a combination of several scientific studies. This process uses novel separation techniques, such as carbon-in-pulp (CIP) filtration and ionic liquid extraction.
The ionic liquid is a key component in extracting Nd and Dy. The ionic liquid forms an organic complex with Nd and Dy, allowing them to be easily separated from the other metals which remain in the aqueous phase using centrifugation. Following this, the REEs must be separated to obtain the individual metals. Nd and Dy are typically very difficult to separate from each other as they possess very similar physical and chemical properties. However, the ionic liquid allows Nd to remain in the organic phase, while reacting Dy with EDTA (ethylenediaminetetraacetic acid) to move Dy from the organic phase into the aqueous phase. This method has been verified several times and gives a high recovery rate for both REEs [2].
CIP filtration is a technique used to extract trace amounts of gold from solution. The gold is first reacted with cyanide. The activated carbon then absorbs the aurocyanide (Na[Au(CN)2]) suspended in solution, and the slurry can then be filtered out. Subsequently we can use electrowinning to plate the gold onto steel wool to recover the pure metal, leaving the carbon and cyanide behind. The process was developed in the 1980s and allows for a high recovery and high selectivity even in the presence of other competing elements.
WHAT MAKES OUR DESIGN SOLUTION EFFECTIVE
Our design takes advantage of a combination of different techniques to recovery the most valuable and prevalent REEs and other metals from hard disk drives (HDD). Physical separation techniques are used in the beginning of the process, including magnetic separation, liquation, and an air separator to remove the majority of impurities from the feed. Then, a series of reactors are used to selectively isolate the metals we want to extract from the feed. These chemical separation techniques eventually result in a precipitate that can be filtered out and further processed; where the gold then undergoes electrowinning, and the Nd, Dy, and Co are thermally decomposed in crucibles.
HOW WE VALIDATED OUR DESIGN SOLUTION
The process uses unconventional methods to obtain a high recovery and high purity (>99.5%) of the separated REEs [2]. Because this process is still being researched and has not been industrially implemented, experimental data on the process and its reagents is limited. Therefore, the design cross-references data from several recent scientific articles to obtain the optimized process conditions (mainly time and temperature), as well as the selectivity and recovery rates for each step in the process. This allows us to obtain the amounts of reactants required, as well as the efficiency of each step for recovering Fe, Co, Nd, and Dy. Therefore, it is recommended that before implementing this process industrially, further testing should be performed to confirm these results.
The gold recovery process is well-documented and has been extensively studied in industry and researched in labs. Data for CIP filtration can be obtained from literature and verified through MATLAB simulations to obtain the reaction kinetics and thermodynamics. Reaction kinetics follow the Arrhenius rate law and first order reaction kinetics.
FEASIBILITY OF OUR DESIGN SOLUTION
The net present value (NPV) of this process was calculated for a 25-year life and 15% discount at $10 million. With a total capital investment of $4.2 million, the payback period is 3.6 years, and the rate of return is 13.5%. The major sensitivities for the economics of this process are the gold price, feed price, and operating expenses. Since this is a recycling process using electronic waste, the feed price is assumed to be $0 per HDD for the base case. In the sensitivity analysis, the feed price was the largest factor in the NPV of the project where, at a price of $7/HDD, the NPV dropped from $15 million to $1.5 million.
REFERENCES
[1] Talens Peiró, Laura, & Villalba Méndez, Gara. (2013). Material and Energy Requirement for Rare Earth Production. JOM (1989), 65(10), 1327–1340. https://doi.org/10.1007/s11837-013-0719-8
[2] Riaño, Sofía, & Binnemans, Koen. (2015). Extraction and separation of neodymium and dysprosium from used NdFeB magnets: an application of ionic liquids in solvent extraction towards the recycling of magnets. Green Chemistry : an International Journal and Green Chemistry Resource : GC, 17(5), 2931–2942. https://doi.org/10.1039/c5gc00230c
Partners and mentors
We want to thank our supervisor and chemical engineering professor, Dr. Anne Benneker, for offering her support and guidance throughout the past 8 months of this project.
Our photo gallery
Process for Dividing the Feed (into Nonmagnetic and Magnetic Streams) and Obtaining the Pure Gold
Process for Obtaining the Iron (III) Hydroxide Product and Separating the REEs and Cobalt from Each Other and Other Impurities
Process for Obtaining the Cobalt (II) Oxide Product
Process for Recycling the Ionic Liquid and Obtaining the Neodymium Oxide Product
Process for Obtaining the Dysprosium Oxide Product