Project Category: Civil

THERE IS A HOUSING CRISIS IN THE CANADIAN NORTH.
OUR GOAL IS TO SOLVE IT.
Space
Come chat with us!
April 5th from 10:00 a.m. to 12:30 p.m.
If technical difficulties arise, please contact kate.alexander1@ucalgary.ca
About our project
PROBLEM
There is a housing crisis in the Northwest Territories and Nunavut. Currently, much of the housing uses the traditional construction that is utilized elsewhere in Canada. Because of the harsh climate of the North, many homes are in poor condition due to material breakdown and mould growth. The remote locations of these communities adds another level of difficulty due to the challenge of material transportation and lack of specialized labour force.
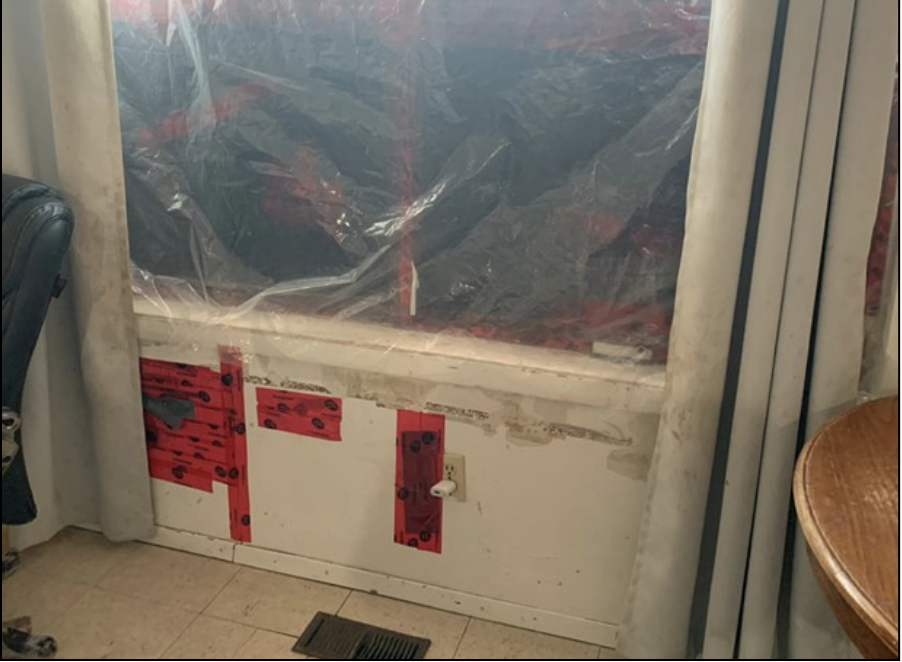
SOLUTION
We have designed an innovative modular housing unit that will be constructed from Ultra High Performance Concrete (UHPC) to maximize durability. These units will be precast and shipped as a whole unit in order to reduce the labour required on site, plus maximize efficiency during the short construction season. Once constructed, these units will serve their homeowners upwards of 50 years.
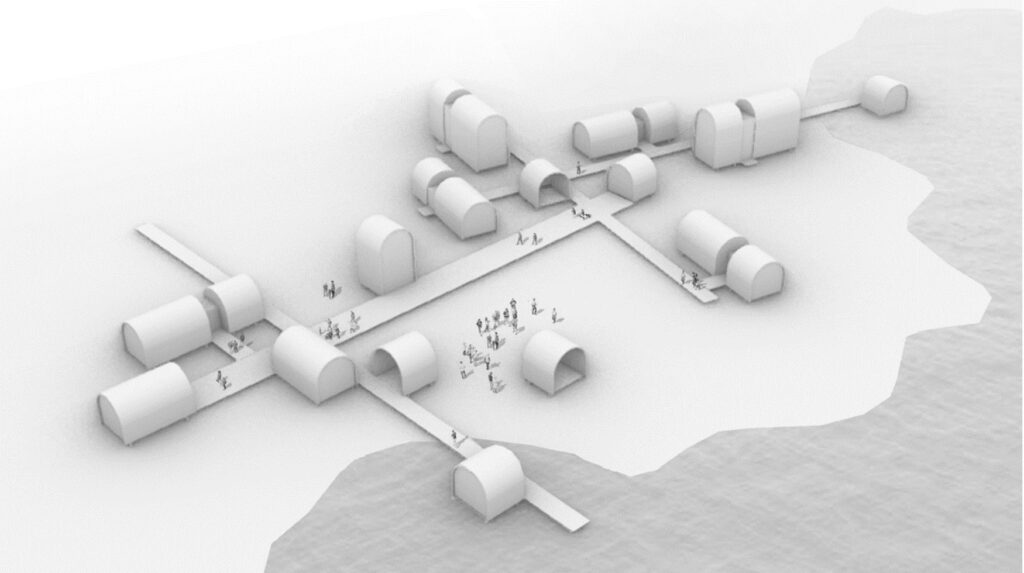
Space
Want to learn more?
Meet the Arctic Design Solutions team
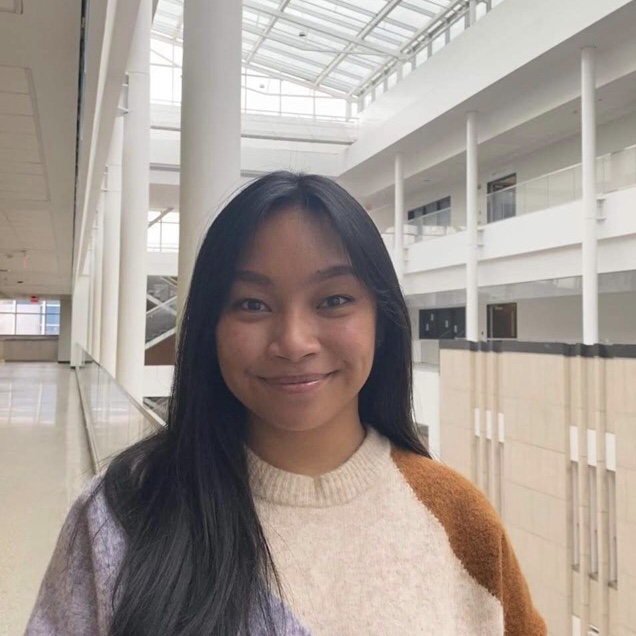
Anne Navalta
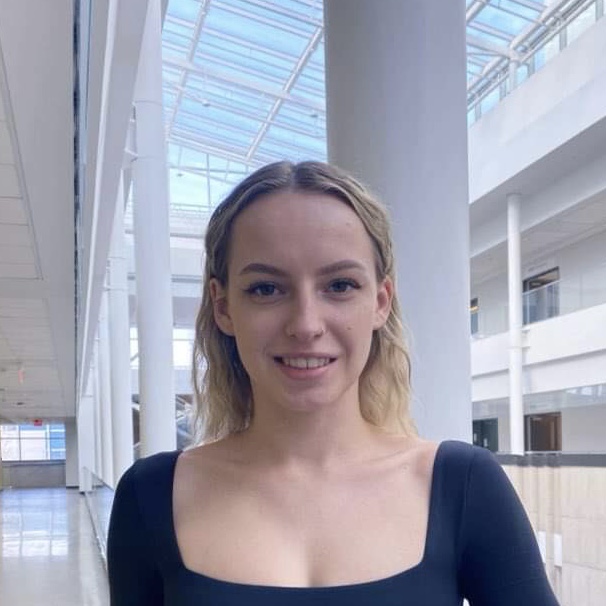
Marie Howell
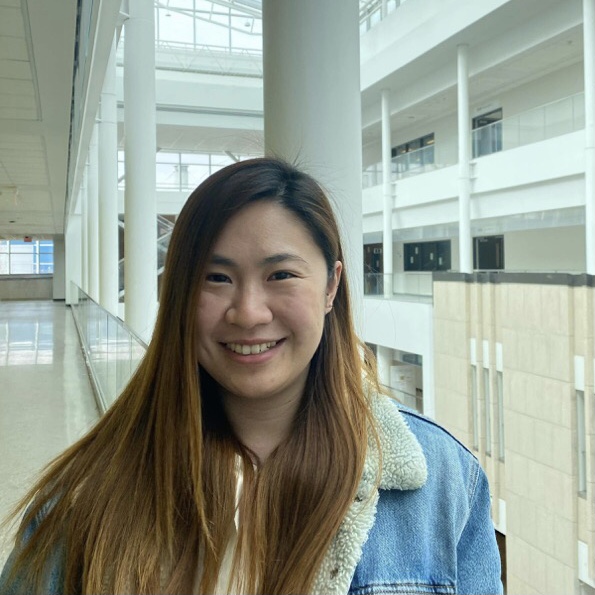
Ivy Hui
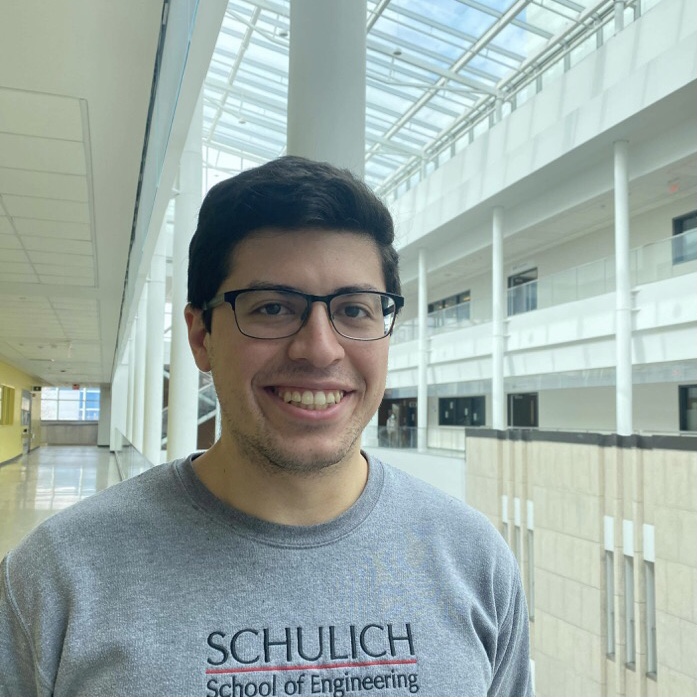
Mateo Velasco

Juan Echenagusia
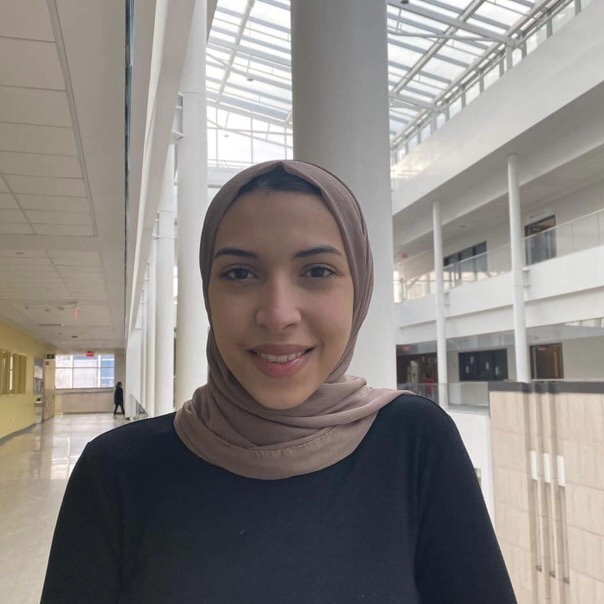
Mona Elsayed

Kate Alexander
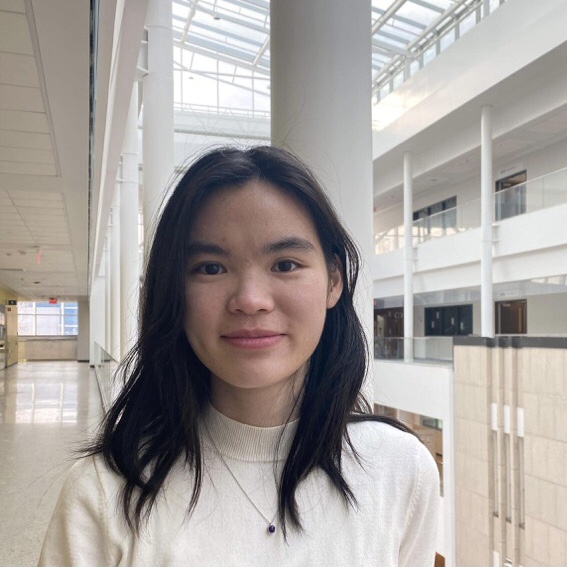
Trisha Truong
Details about our design
OUR DESIGN SOLUTION
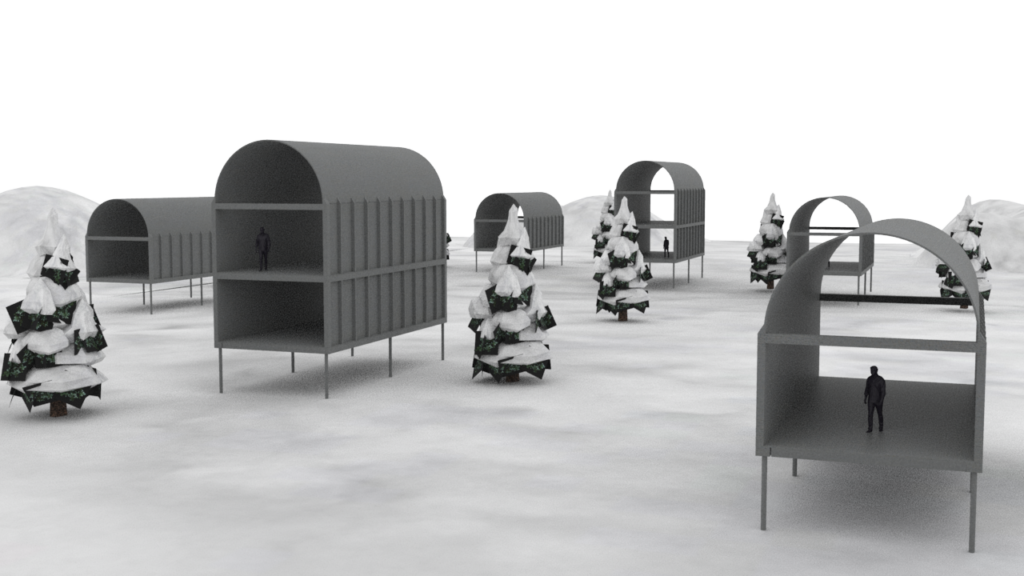
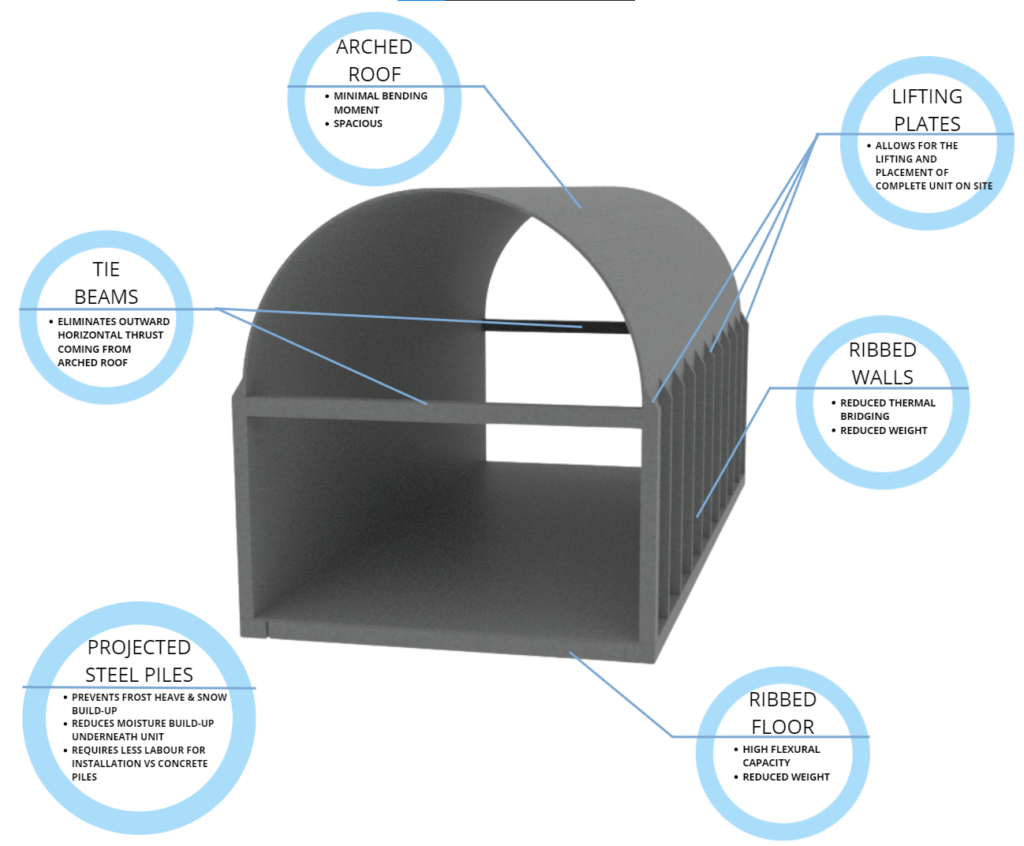
HOW OUR DESIGN ADDRESSES PRACTICAL ISSUES
Our design addresses 3 major issues:
1. Current Housing Conditions
Current construction standards have proven ineffective in the climate of the Northwest Territories and Nunavut. Some of these effects can be seen in the photos below.
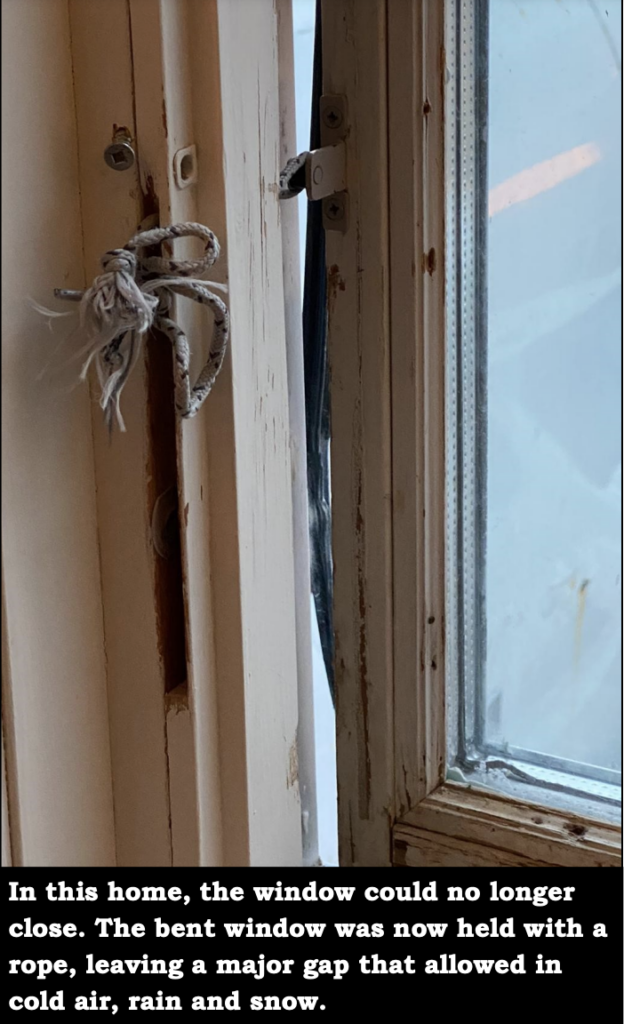
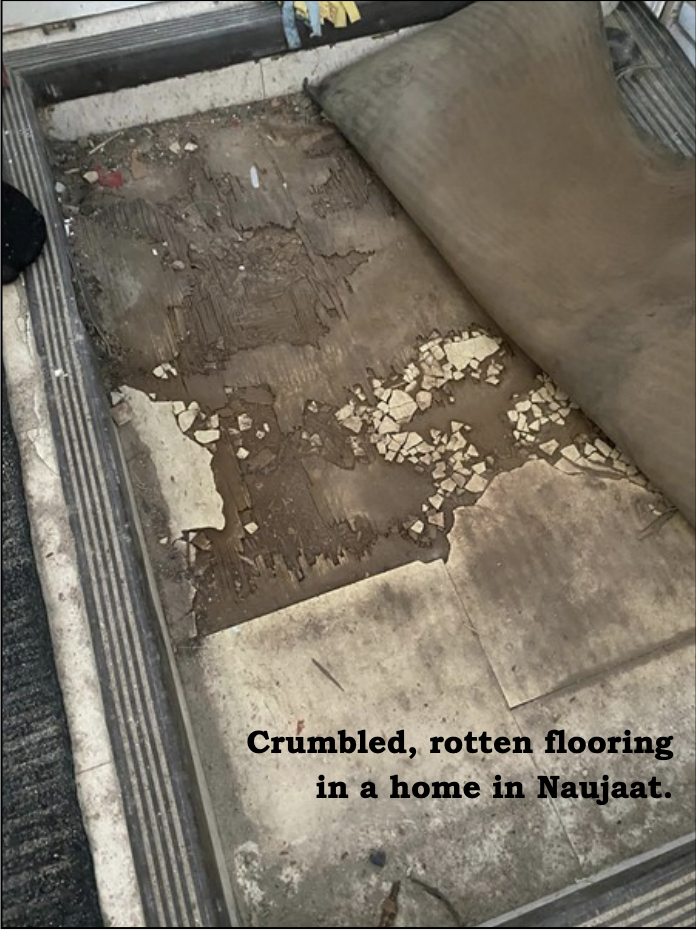
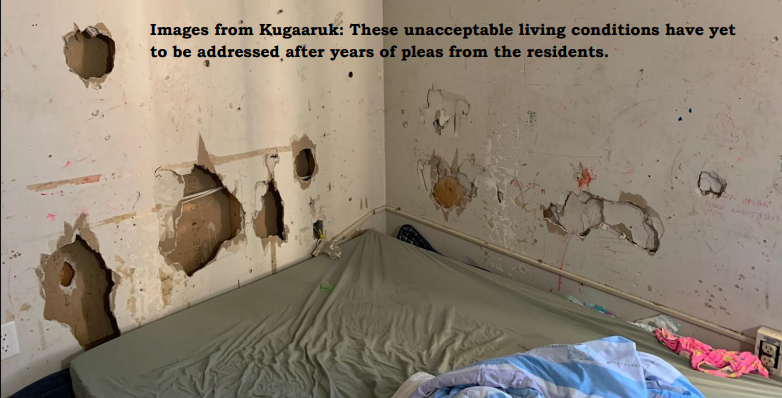
2. Housing in Short Supply
There is a significant need for government funded housing. For example, in the community of Taloyoak, NU, there are 206 public housing units, with a current wait list of an additional 112 households [1].
The graphic below shows statistics about the living conditions of Nunavut residents. An effective modular housing solution is essential for improving their quality of life.

3. Construction Challenges
Permafrost is a major issue that complicates construction in the Northern climate. Our design uses piles in order to remain structurally sound even with the effects of permafrost.
The North has a short construction season. By creating a precast design where units are completely assembled prior to delivery, more housing can be built during the short season.
There is a lack of skilled labour force in most Northern communities. Because of this, construction requiring specialized trades is very expensive and can take a long time. By building the units in the south, we can avoid these issues.
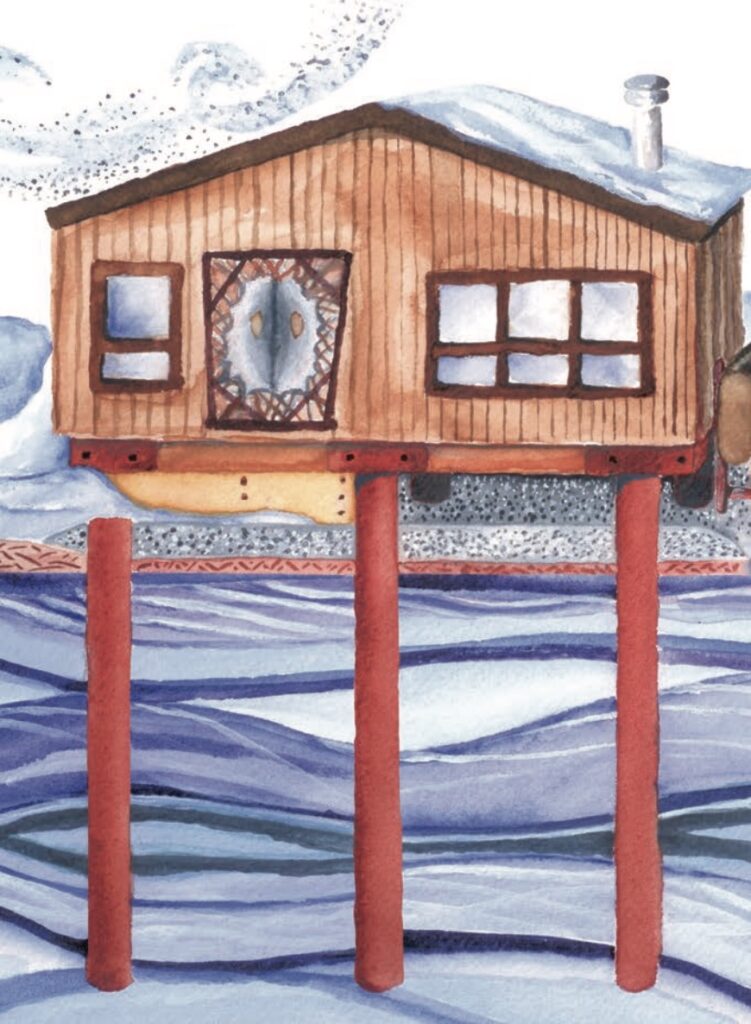
WHAT MAKES OUR DESIGN INNOVATIVE AND EFFECTIVE
Materials
Unlike previous housing solutions that have utilized construction meant for warmer climates, our design has been specifically made to meet the durability requirements for the climate in the Territories. Our design uses Ultra High Performance Concrete (UHPC) and Glass Fibre Reinforced Polymer (GFRP).
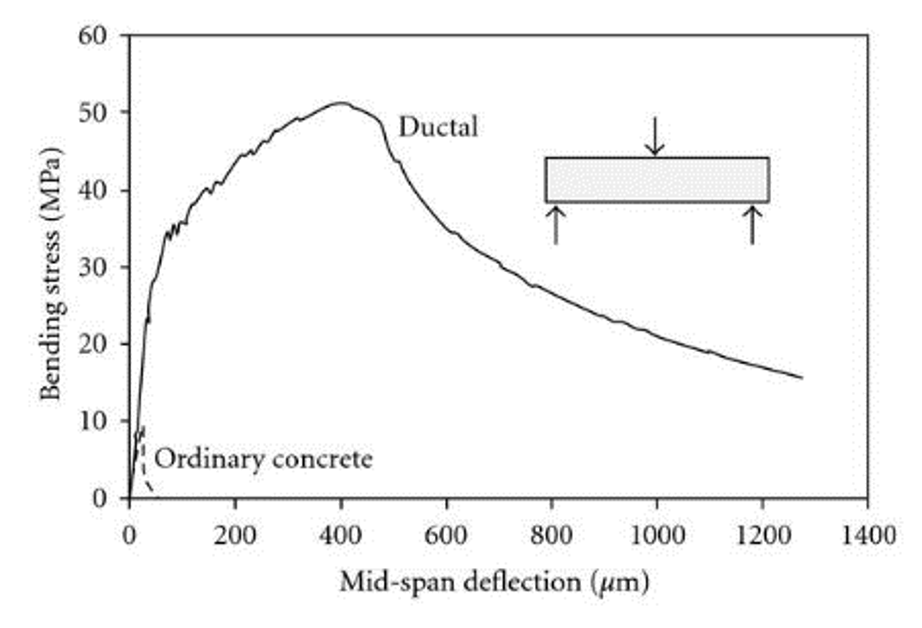
Steel will rust. Wood will rot. UHPC will withstand upwards of 50 years in the North.
Our biggest design constraint was the weight of the unit. Due to the poor conditions of many roads in the Territories, the full unit is limited to 21 tonnes for transportation purposes. By using UHPC and GFRP, we are able to use much less material than if we were using conventional concrete. This allows the design to meet this constraint.
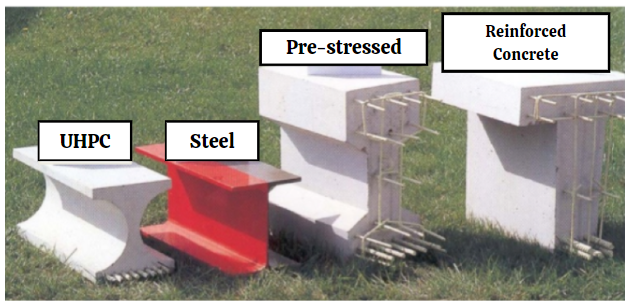
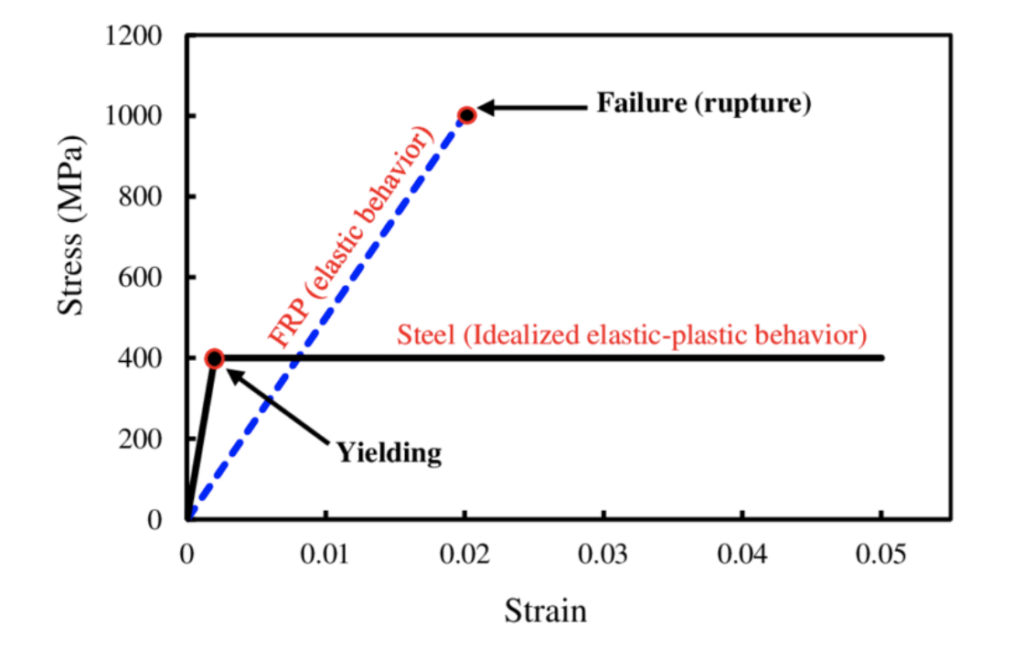
Modularity
The modularity of our design is an innovative solution to provide flexibility for various household types. By designing them to be able to stack or placed side-by-side, we include the flexibility needed to accommodate large or multi-generational families living under one roof. Units can also be added or removed as household needs change. This is key because it can alleviate the overcrowding issues plaguing social housing in the Territories.
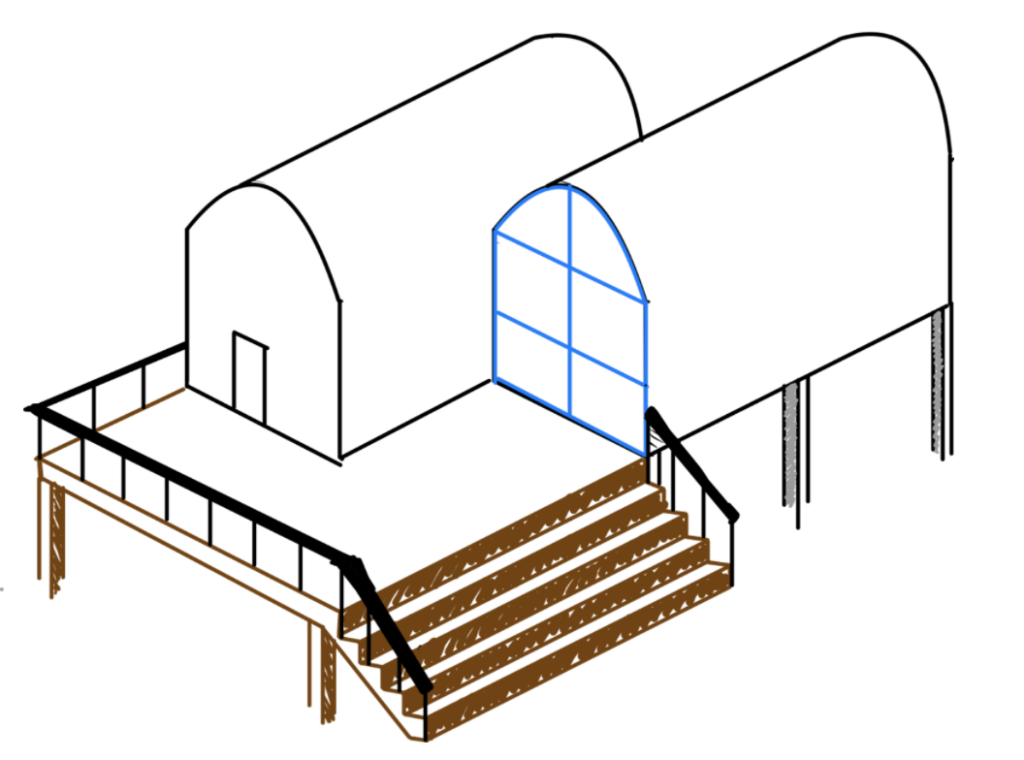
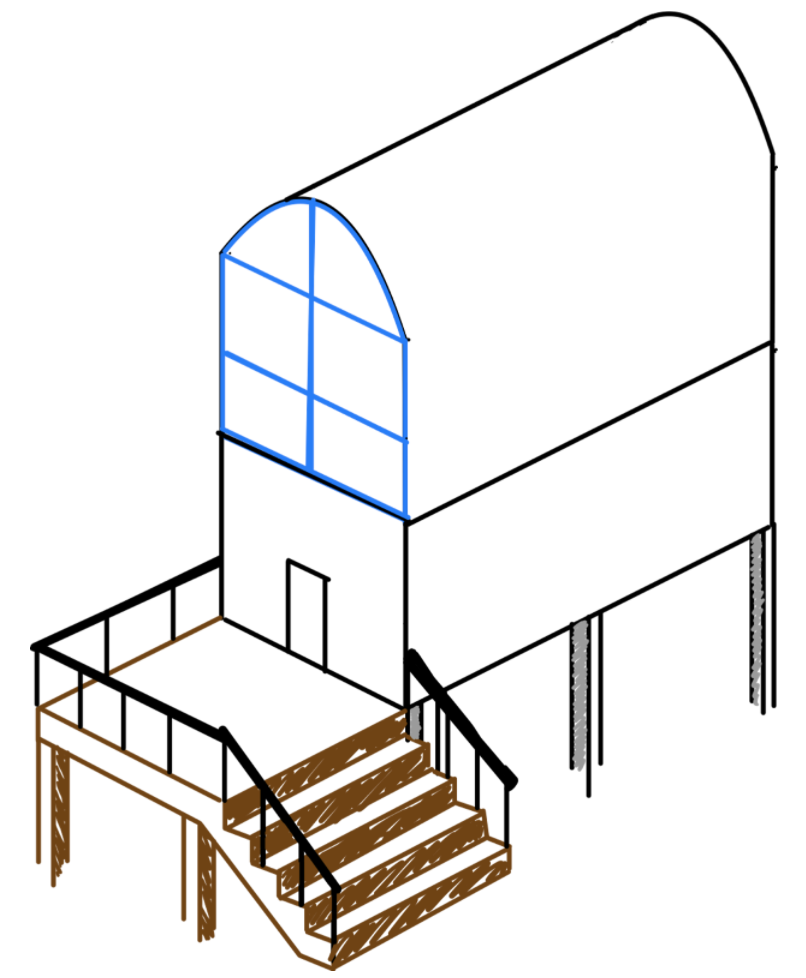
WHAT MAKES OUR DESIGN SUSTAINABLE
Sustainable housing means “healthy, affordable, flexible, and environmentally responsible housing […] that is culturally appropriate to the needs of the users.” [7]
Space
DURABILITY
spa
Space
FLEXIBILITY
Space
Space
Space
Space
Space
Space
Space
Space
Space
REDUCING HEATING COSTS
Space
Space
Space
Space
Space
Space
Space
Space
INVESTING IN THE COMMUNITIES
Achieved using Ultra High Performance Concrete combined with Glass Fibre Reinforced Polymer reinforcement. We aim for the houses to last 50+ years to reduce the cost and need for maintenance.
Space
The modularity of our design will mitigate the risk of overcrowding as the unit configurations can vary depending on the needs of each household. The owners can select a configuration to suit their needs. Below are examples of possible configurations.
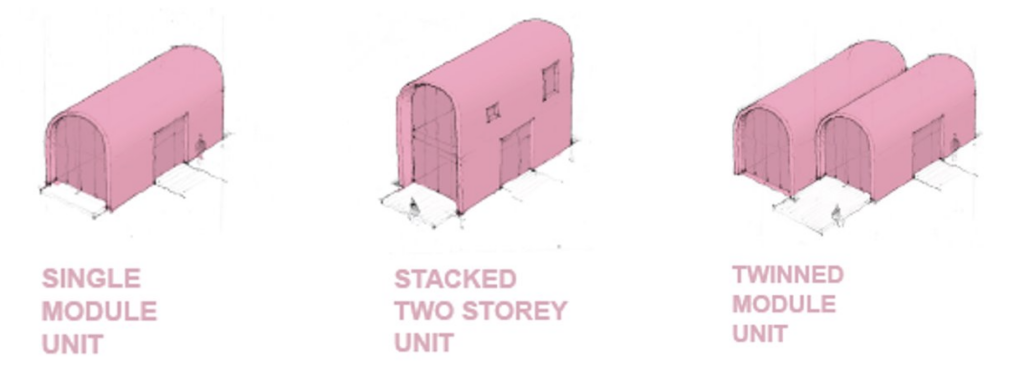
Space
Our design eliminates thermal bridging by ensuring there are no gaps in the insulation or connections. This drastically lowers the heating costs to compensate for heat loss in the units during extreme cold temperatures.
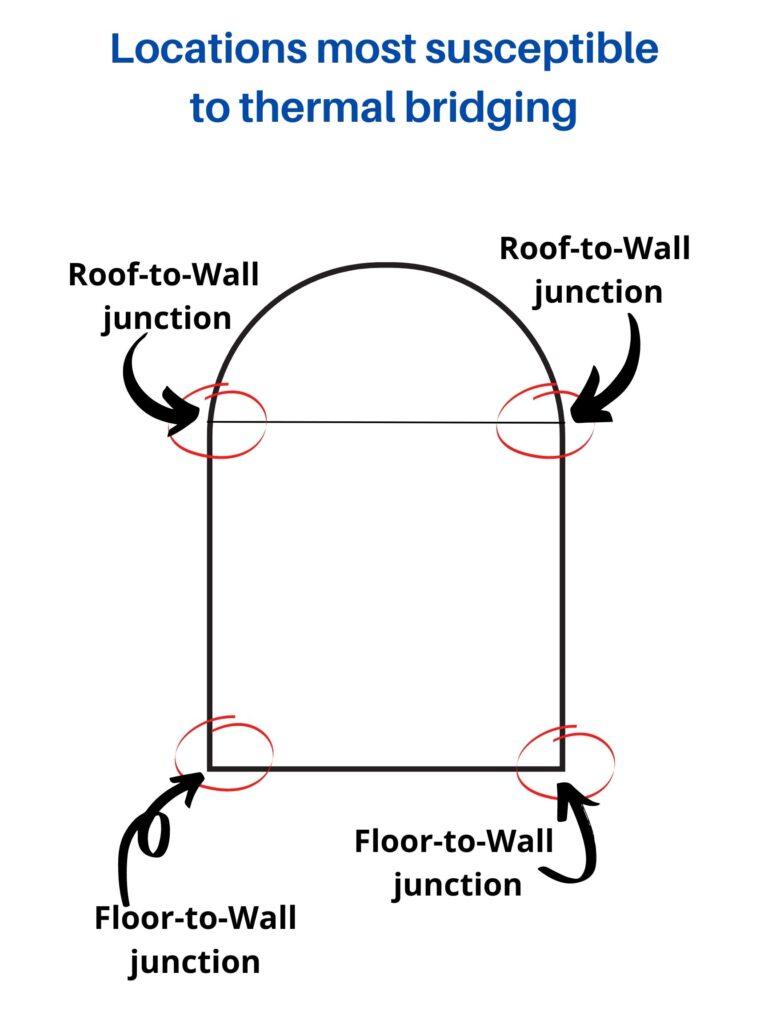

Our aim is to invest in the capacity of local communities during the deployment and maintenance of the project. This includes providing training opportunities for local labour for any on-site construction and maintenance of the units which will reduce operational costs in the long run.
HOW WE VALIDATED OUR DESIGN SOLUTION
We have used the following codes and standards to validate our design:
• The National Building Code of Canada was used to determine critical loading and load combinations
• The Canadian Concrete Design Handbook was used to guide the selection of member sizes and reinforcement for flexural, axial, and shear resistance
• Design Guidelines for RPC Prestressed Concrete Beams were used to adjust the design process from normal concrete to UHPC
• Reinforcing Concrete Structures with Fibre Reinforced Polymers were used to adjust the selection process for reinforcement from standard steel to GFRP
• The Precast Handbook was used to design lifting points to move the units by crane for transportation and installation purposes
Space
After designing the unit by hand, the calculations were validated using the computer program, SAP. The following are some SAP outputs from our load cases.
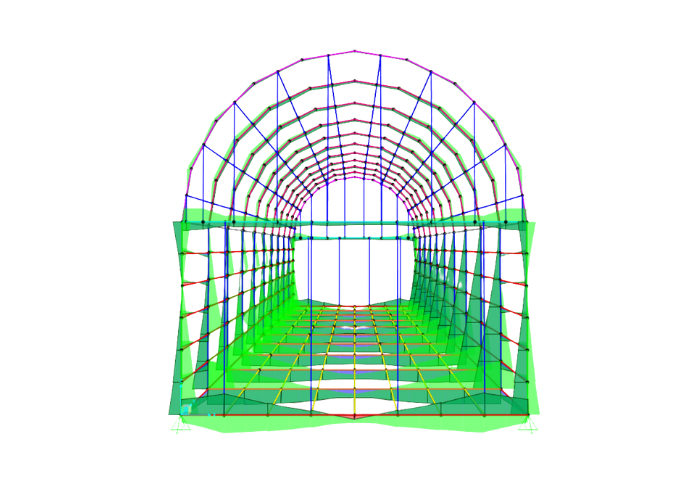
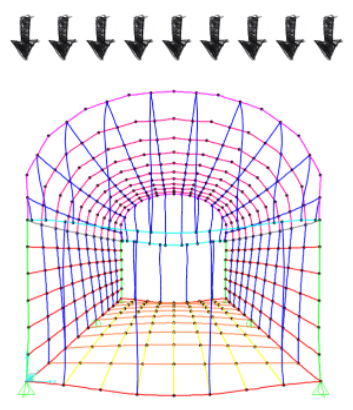
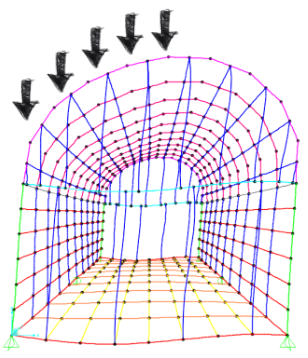
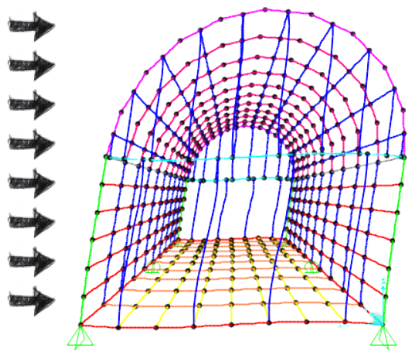
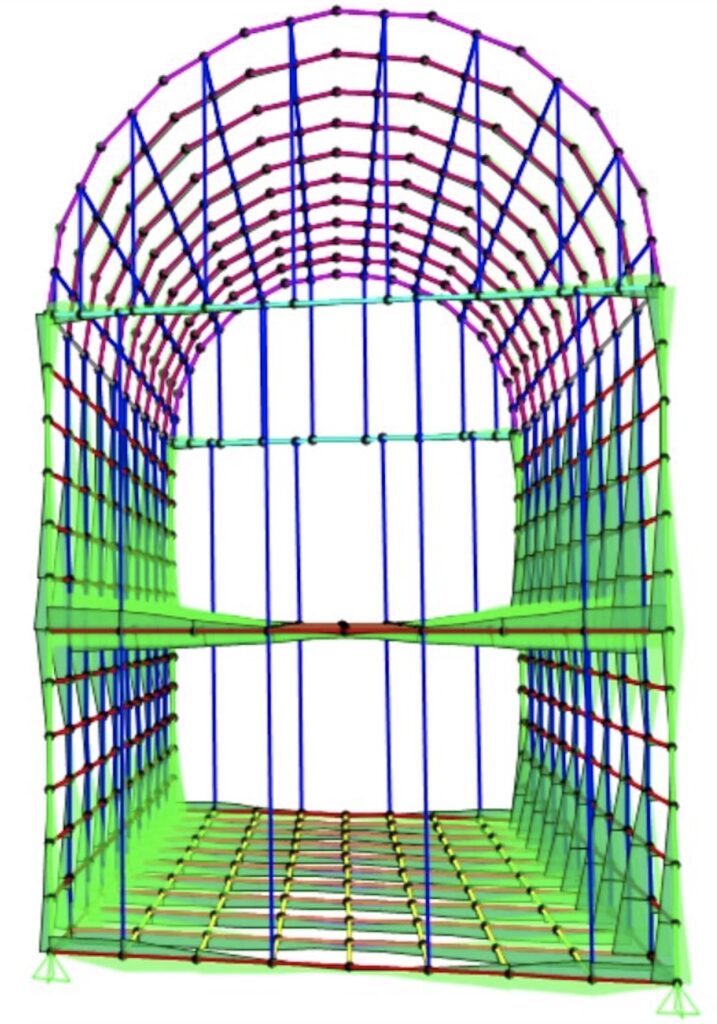
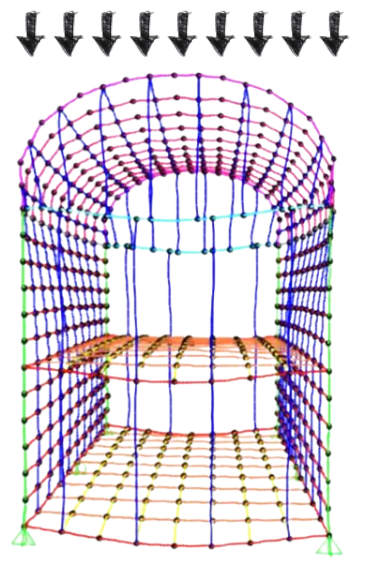
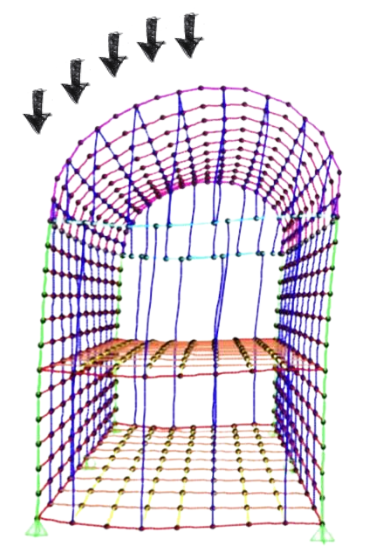
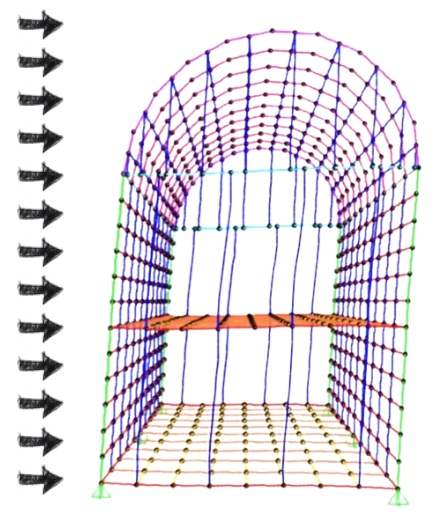
FEASIBILITY OF OUR DESIGN SOLUTION
Logistics
Our design addresses all stages of the project including construction, shipping, shipping, assembly on site, and maintenance.
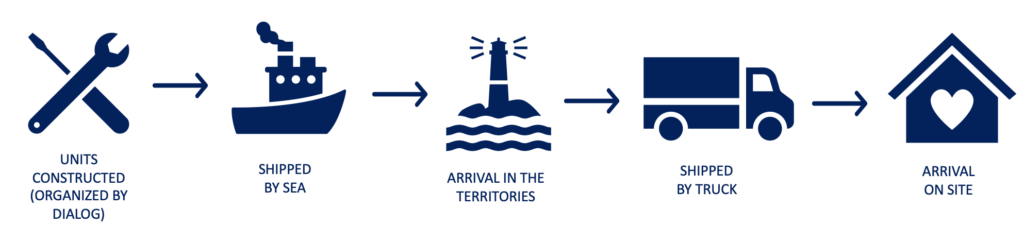
Cost Estimate

The total cost of the materials is approximately $25,000 CAD per unit. Transportation is heavily dependent on the location of each unit. The units will be constructed in a purpose-built factory. However, the details of this have not yet been finalized and therefore labour cannot yet be estimated.
Partners and mentors
We want to thank the many people who helped us with this project, especially our academic advisor Dr. Neil Duncan and our industry advisor Mr. Gamal Ghoneim from DIALOG.
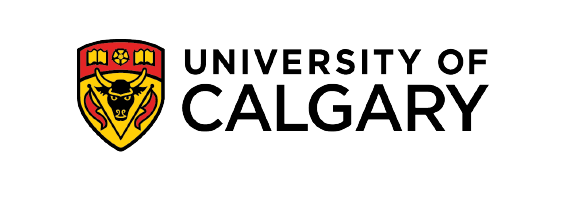
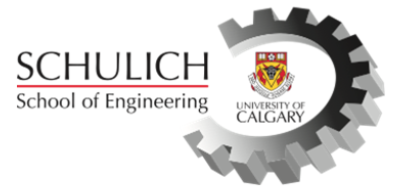

Our photo gallery
DETAILED DESIGN DRAWINGS
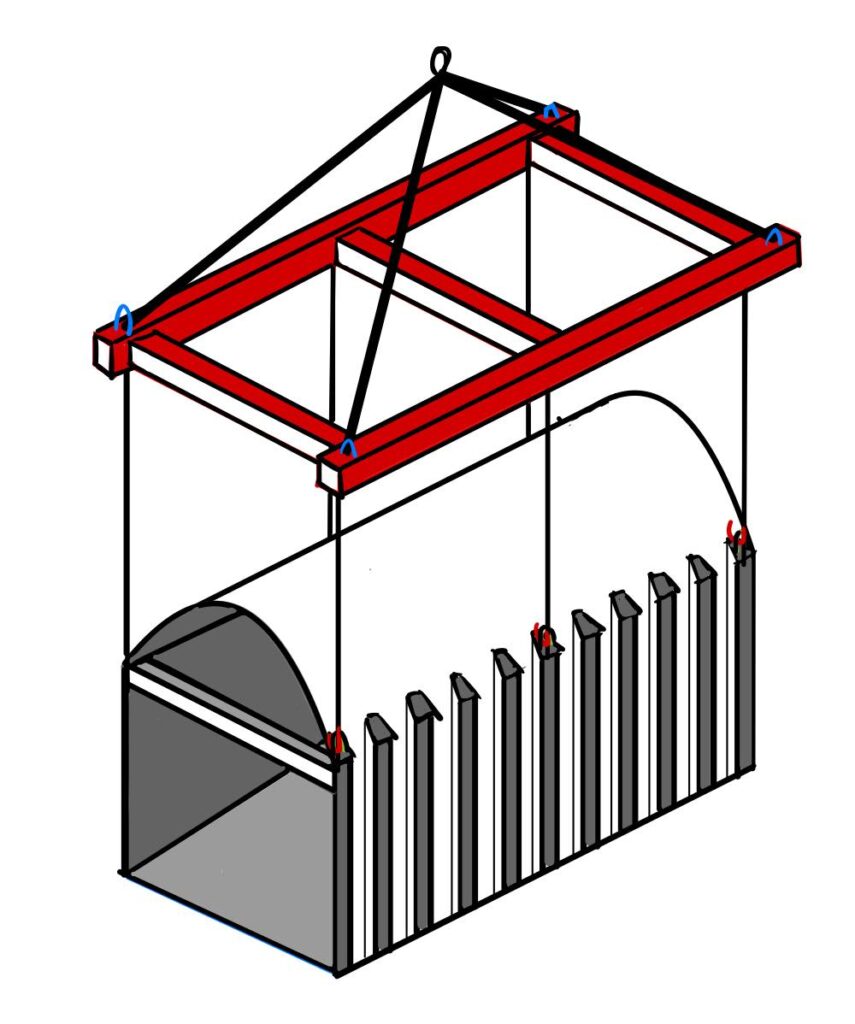
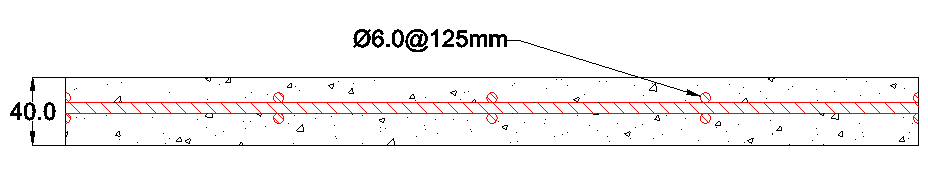
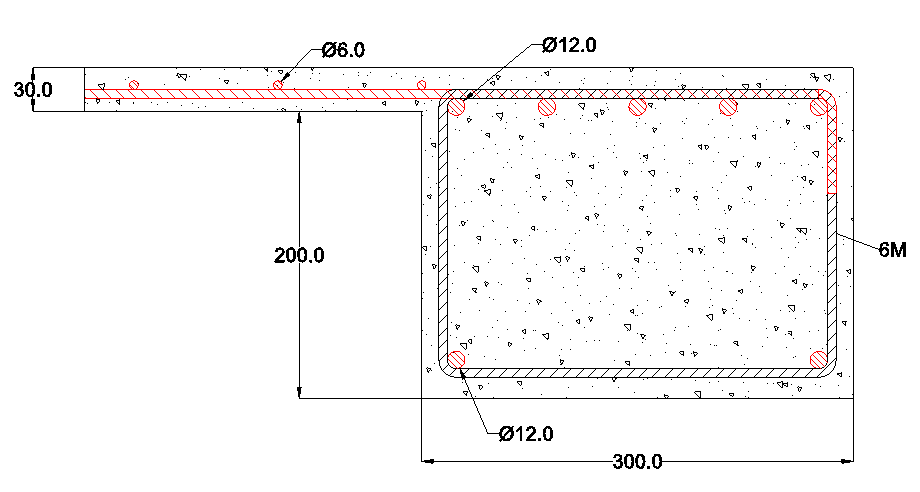
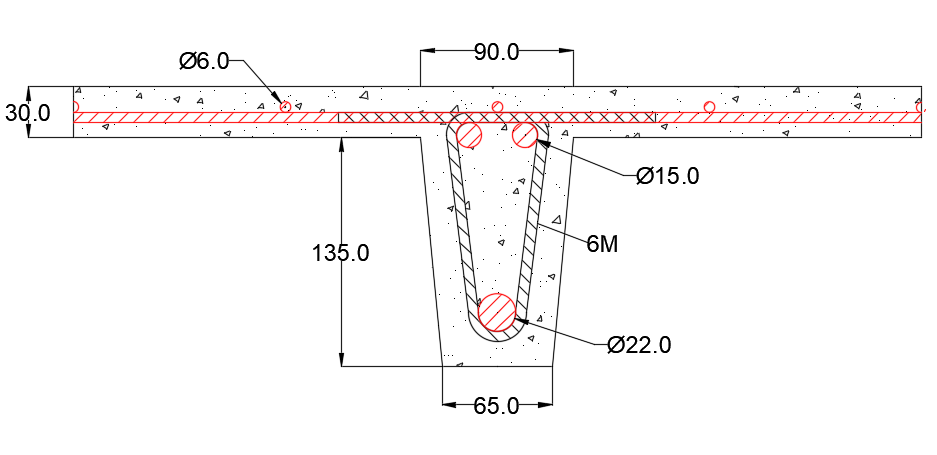
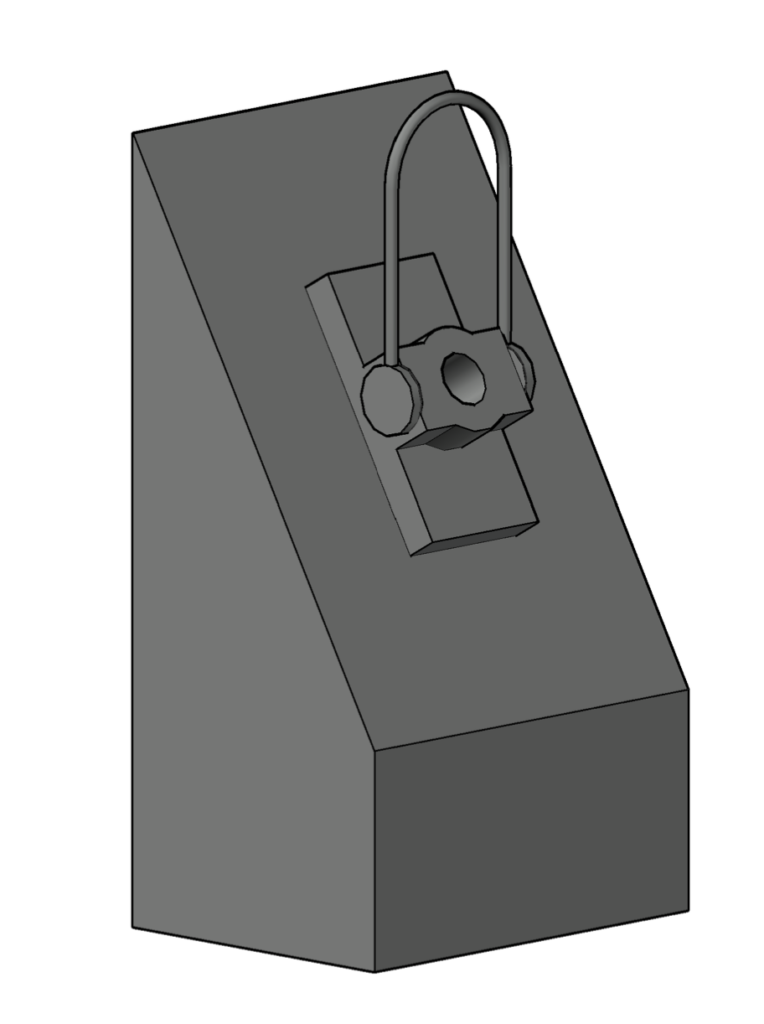
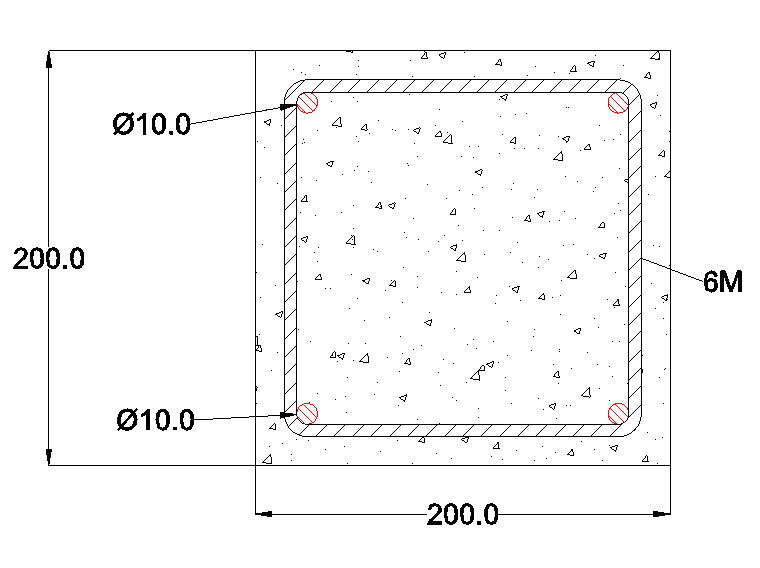
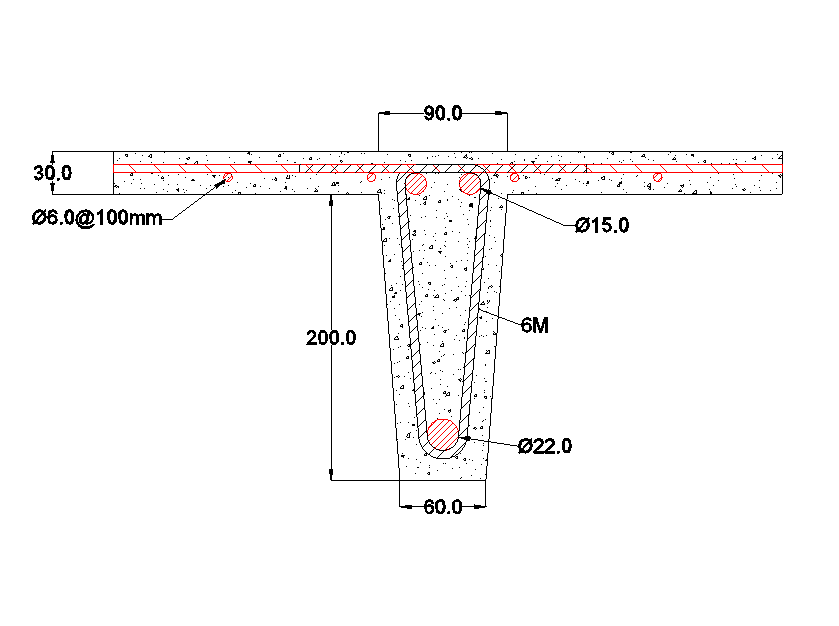
UHPC APPLICATIONS

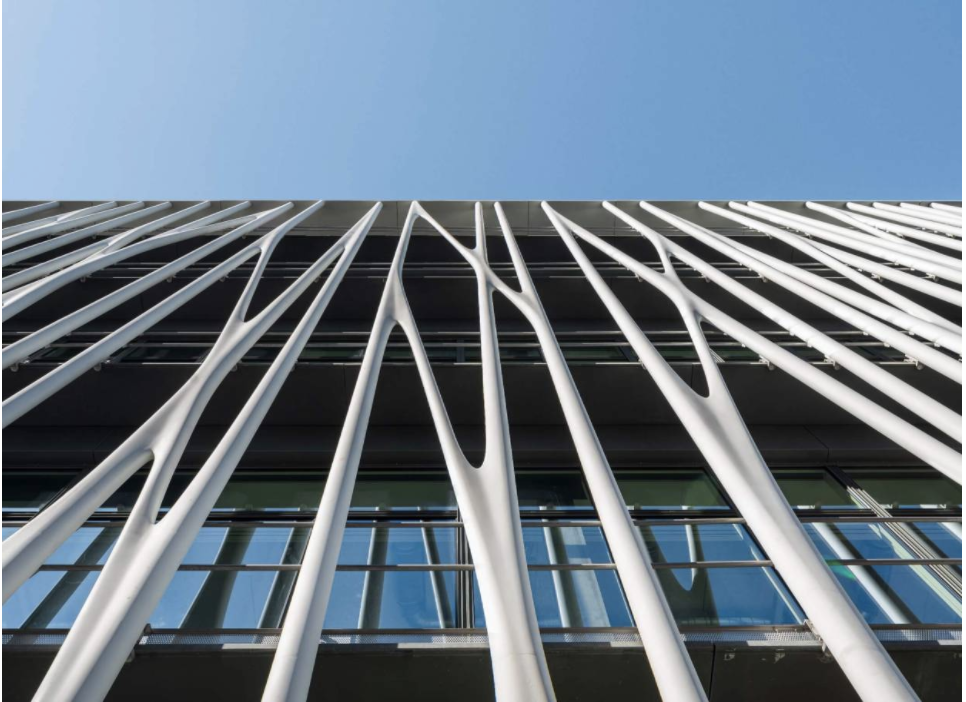

PRELIMINARY DESIGNS
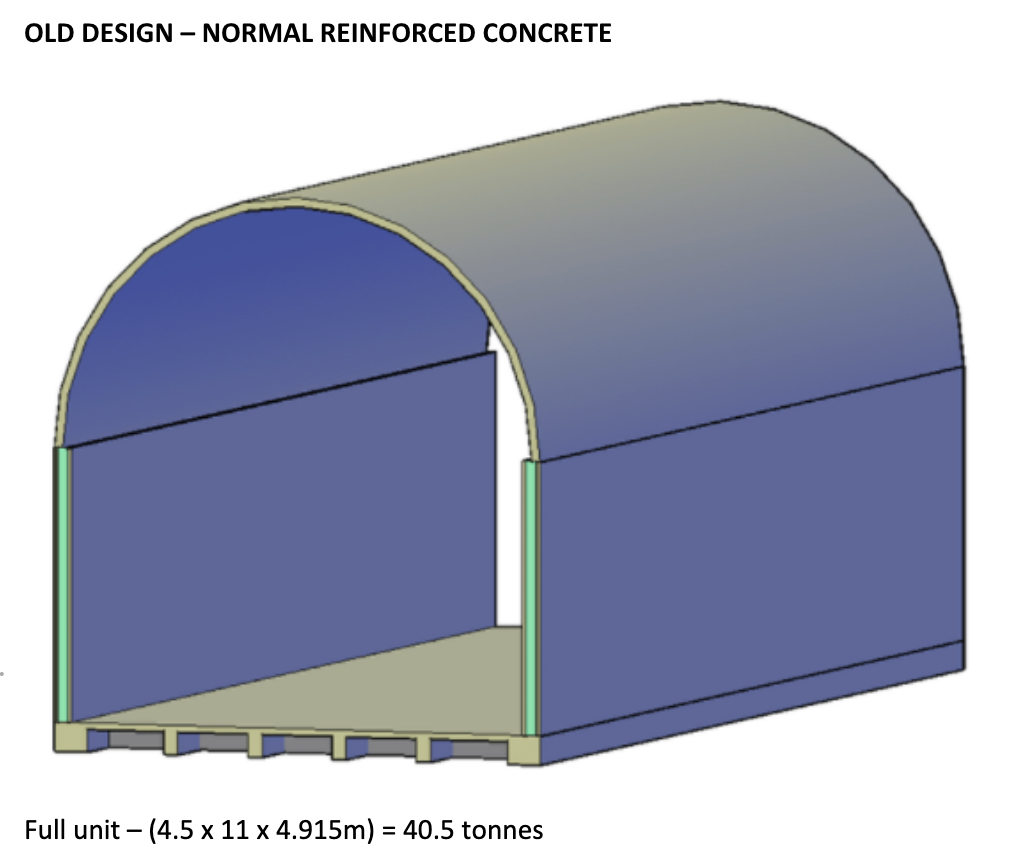
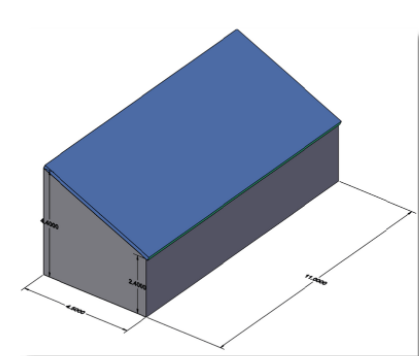
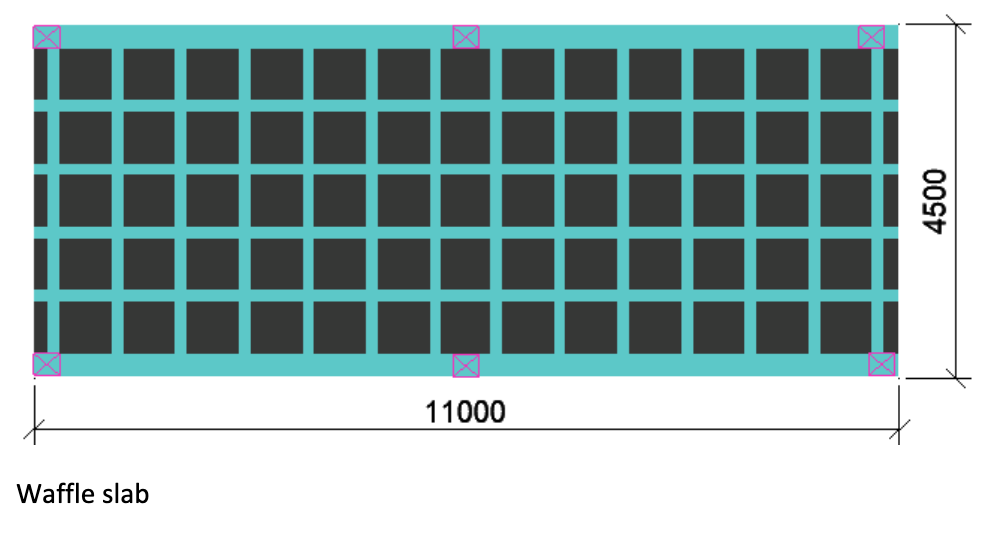
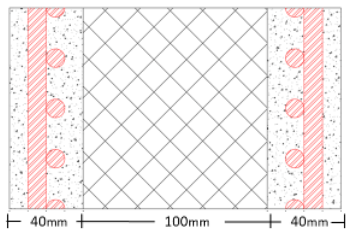
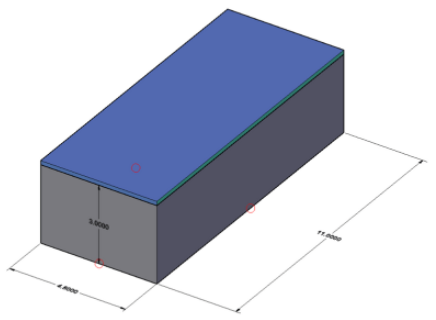
References
[1] M. Qaqqaq. “‘Sick of Waiting’ A Report on Nunavut’s Housing Crisis by Mumilaaq Qaqqaq MP for Nunavut.” 2021. [Online]. Available: https://www.aptnnews.ca/wp-content/uploads/2021/03/Qaqqaq.HousingReport.2021-1.pdf, [Accessed Mar. 14, 2022]
[2] “Nunavut is facing a severe housing crisis.” Mar. 2016. [Online]. Available: https://assembly.nu.ca/sites/default/files/TD%20158-4(3)%20EN%20Nunavut%20is%20Facing%20a%20Severe%20Housing%20Crisis.pdf, [Accessed Mar. 22, 2022]
[3] “A Homeowner’s Guide to Permafrost in Nunavut.” 2013. [Online]. Available: https://www.climatechangenunavut.ca/sites/default/files/permafrost_nunavut_eng_reduced_size_0.pdf, [Accessed Mar. 20, 2022]
[4] “Use of UHPC in Bridge Structures: Material Modeling and Design.” 2012. [Online] Available: https://www.hindawi.com/journals/amse/2012/319285/fig2/, [Accessed Mar. 22, 2022]
[5] G. Holbrook. “Constructing the Future with Ultra-High Performance Concrete.” Dec. 20, 2016. [Online]. Available: https://www.asce-pgh.org/Blog/4468471, [Accessed Mar. 22, 2022]
[6] H. Ibrahim. “Stress-strain relationship for GFRP and steel reinforcement.” [Online]. Available” https://www.researchgate.net/figure/2-Stress-strain-relationship-for-GFRP-and-steel-reinforcement_fig1_328583173, [Accessed Mar. 28, 2022]
[7] Semple. “Learning from others report – Turn back the tide.” 2013. [Online]. Available: https://www.turnbackthetide.ca/files/resources/learning-from-others-report.pdf, [Accessed Mar. 27, 2022].
[8] K. Singh. “What is thermal bridging in construction? How is it prevented?” Oct. 30. 2021. [Online] Available: https://www.engineeringcivil.com/what-is-thermal-bridging-in-construction-how-is-it-prevented.html, [Accessed Mar. 28, 2022].
[9] K. Hanson. “UHPC Offers Endless Possibilities.” Nov. 24, 2014. [Online]. Available: https://precast.org/2014/11/uhpc-offers-endless-possibilities/, [Accessed Mar. 23, 2022]
[10] “Archistructure: Unwavering Strength, Uncompromised Aesthetic.” [Online]. Available: https://www.ductal.com/en/archistructure, [Accessed Mar. 27, 2022]
[11] “Materials for Design.” [Online]. Available: https://www.materialsfordesigninc.com/caast-uhpc.html, [Accessed Mar. 28, 2022]