The NGR Level One Sensing System
Project Category: Electrical
About our Project
In engineering, what is more important than safety? Thanks to Approach Controls Inc., Team Level-Up has been tasked with a project to create a system to automatically sense the liquid level, volume and rate of change in their client’s chemical totes. Not only will this reduce the effort to take manual liquid measurements, but it will also ensure that operators out in the field are safe from highly acidic or volatile liquids. In just eight months, our team of five electrical engineering students have sourced help from experienced mentors, engineers, and technicians to design and prototype a sensing system where the operator places a sensor at the top of the tote and the data received gets wirelessly transmitted back to their data van. The system is also complete with its own power source and user interface for operators out in the field to easily view and obtain liquid height, volume and rate of change measurements. Given our short time frame, we hope you find the work we have done as a start to a continuously improving product.
Please read note located in the video description.
Project Photo Gallery
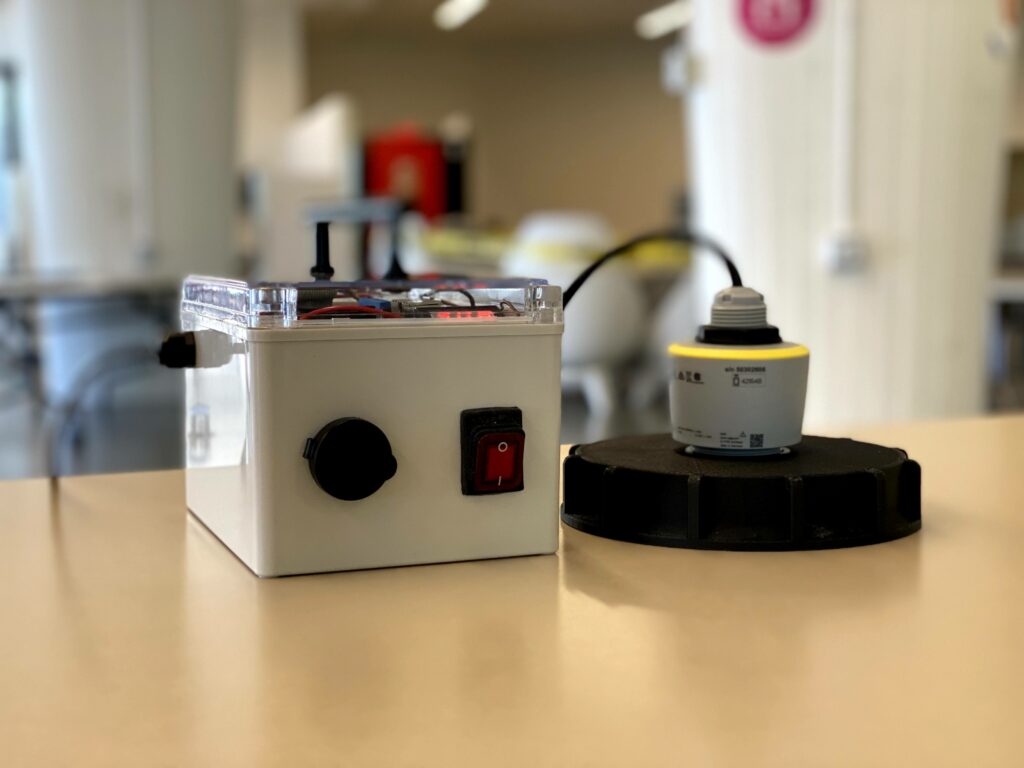
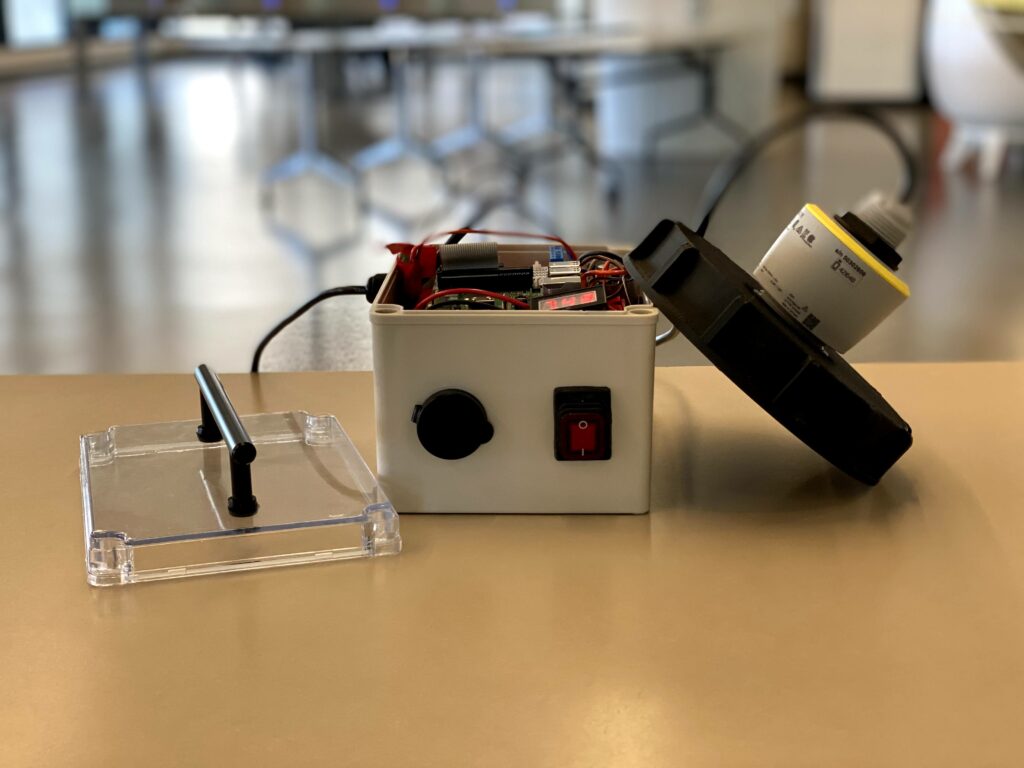
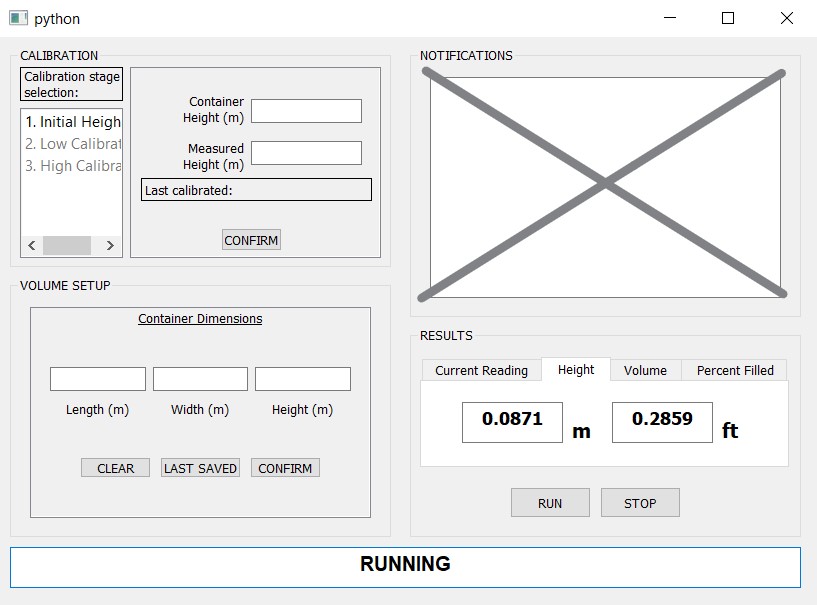
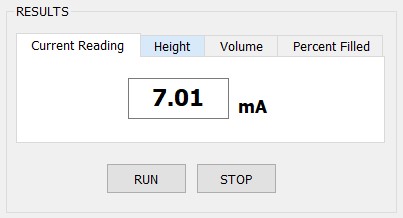
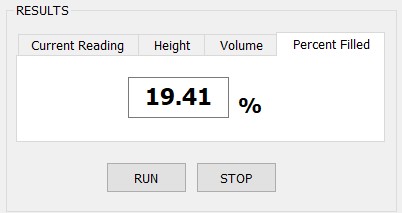

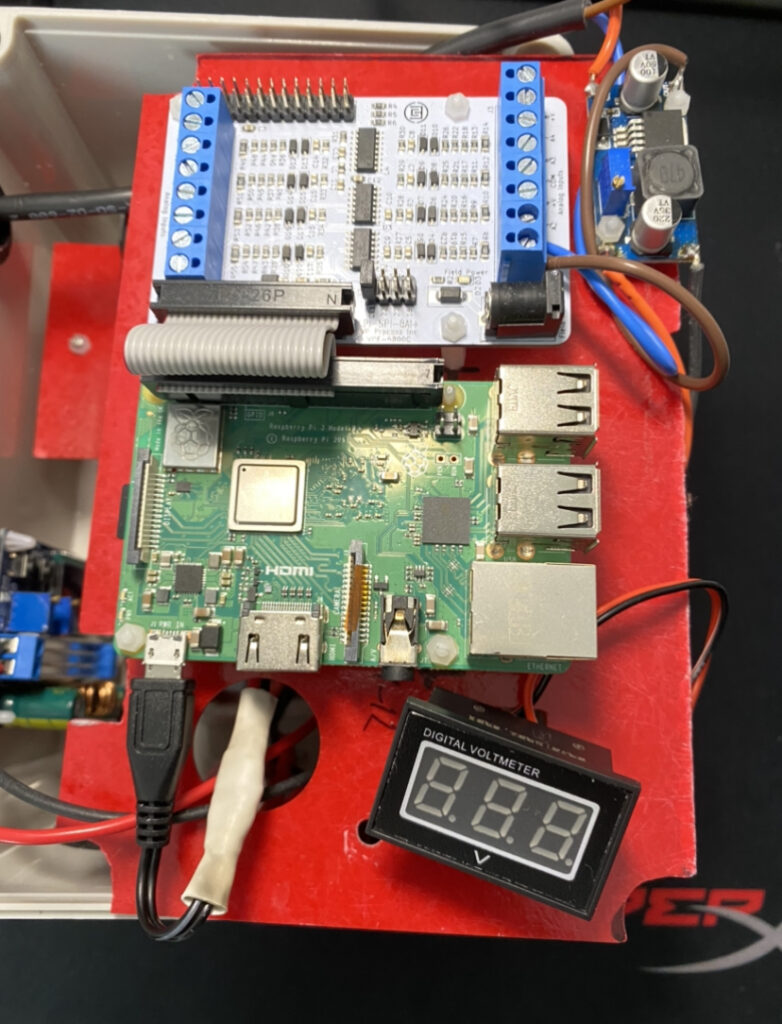
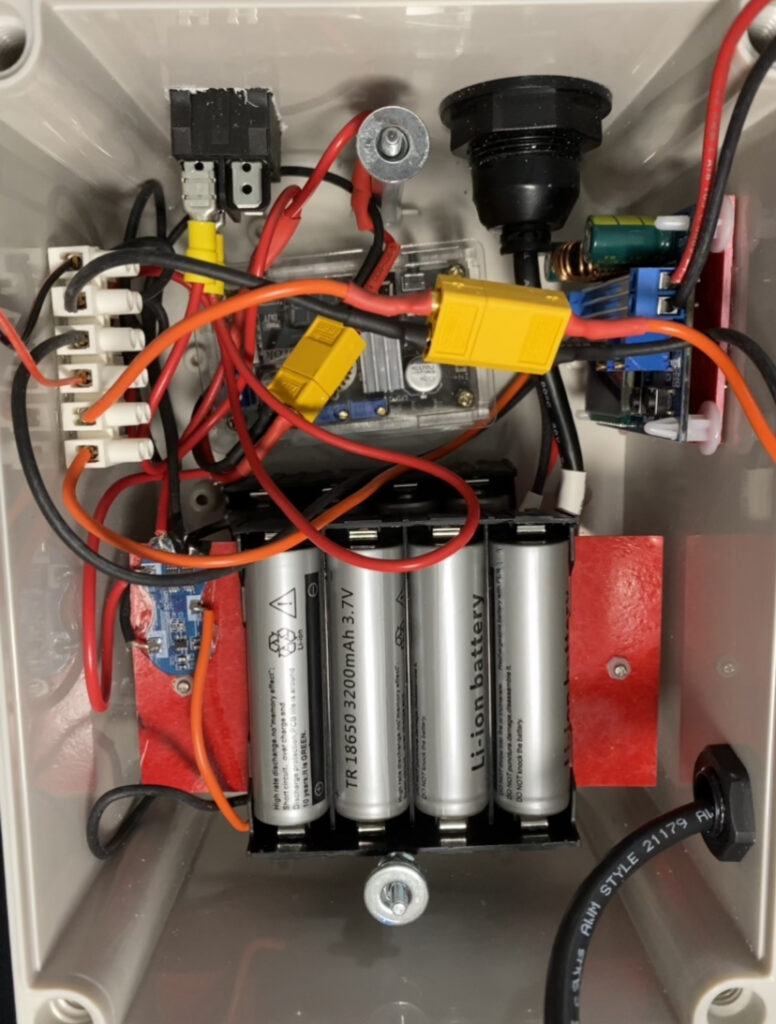
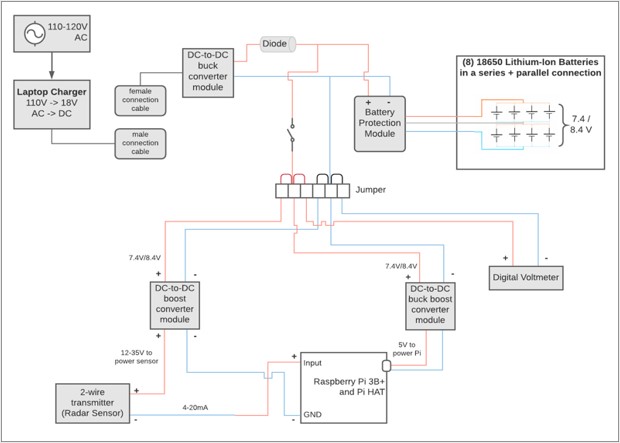
Details About our Design
HOW OUR DESIGN ADDRESSES PRACTICAL ISSUES
The currently used method of measuring liquid level is the traditional dip stick method where an operator dips a stick into a chemical tote and the mark that the fluid makes on the stick gets translated to a height. This height is conveyed back to the operator in the data van. Our design addresses three major issues regarding the dipstick method which are present in the industry.
The first and, arguably, the most important issue is the safety of the operators. Operators often encounter heavily acidic or volatile liquids and using the dipstick method means they are within splashing distance. Since the sensor is just placed at the lid of the chemical tote, the operator does not need to stick anything inside to get a reading. The second issue we tackle is the accuracy of the reads being relayed back to the data van. Instead of relying on the human eye to read the marking made on the dipstick, our design uses technology to get liquid level heights with an accuracy of about 0.5 cm. The third issue our design addresses is the tedious nature of the current protocol for taking a measurement. If a measurement from a specific tote was needed, an operator would have to go all the way to the tote, take the measurement, and radio it back to the data van. With our design, the measurements are being wirelessly transmitted to the data van about every second. This eliminates the need for the operator to take measurements at every hour.
WHAT MAKES OUR DESIGN INNOVATIVE
Currently, the industry standard method for measuring substance levels in containers is the classic dip-stick method. This method is quite dated, having weaknesses in safety, accuracy, ease, and cost among other things. The dip stick must be handled by an operator, who may potentially be exposed to harmful effects from the substance. With continuous measurements, it also becomes increasingly more likely that the accuracy will be lesser compared to an automated system. It also becomes more tedious, with ongoing costs associated with the labor.
Our design innovates on this issue, providing a way for users to receive continuous liquid level measurements in IBC totes safely and consistently. Integrating an industry leading non-contact level sensor with the hardware in the enclosure, we use MQTT communication to allow remote measurements without potentially exposing the user to harm. We emphasized portability, giving the design its own independent chargeable power supply to last a maximum of 7 hours, increasing its usability and reducing the labor required to maintain operation. This gives us a significant advantage considering the typical level sensor would be installed and immobilized within a singular industrial tank.
WHAT MAKES OUR DESIGN SOLUTION EFFECTIVE
An important aspect that makes the design solution effective is the customers’ need to innovate existing methods to be safer and easier was understood and was thought about at every step of the design process. At the start there were many discussions with the customer which resulted in a good understanding of the needs and wants and from there the design process began. At every step of the design process the question of “Will this benefit the customer and user or will it confuse them” was asked, this question was very helpful in keeping us on the right track and to move towards a concrete solution to the best of our ability. Understanding the customer’s wants and needs is a major aspect when it comes to design and this design is no different.
HOW WE VALIDATED OUR DESIGN SOLUTION
To ensure the validity of our design solution and that it satisfies the requirements of the customer, we researched many different options to address the requirements and presented them to the customer to ensure that our design solution was in line with their idea prior to commencing the design process. In our design, every component included is well thought out to produce a product that not only would accommodate all the customer’s needs, but also improve on them.
Our design solution was also subjected to a series of tests to ensure that it is working and that it performs the tasks required. Each test was conducted multiple times to ensure accuracy and repeatability. The hardware, software and mechanical portions of the product were all tested individually before integrating them together. After all the parts were combined, the product once again went through a testing phase to check if the integration was a success and that it is functioning properly and accomplishes what the customer requires.
FEASIBILITY OF OUR DESIGN SOLUTION
The main goal of our NGR Level One Sensor is to provide safety, ease of use, and practicality to the user. To reduce the number of manual steps taken to read measurements, our team decided to choose a solution that will automate the process as much as possible without compromising its value.
To ensure safety:
Our design is a non-contact radar device which means operators will no longer come in close contact with liquids some of which may be harmful or volatile.
To ensure ease of use by the operator:
Our design is very portable and can be easily carried around from one tank to the other. The product also comes with a customized lid which means that the process of continuously screwing on/off a lid will be eliminated. Readings can be measured/monitored from the comfort of the data van as opposed to stepping outside every time a new measurement is required. To monitor the readings, our designed Graphical User Interface (GUI) is very straightforward, minimalistic, and easy to use/understand.
To ensure practicality when out in the field:
Our design has a very rugged enclosure rated at IP67, and a sensor rated at IP66/68. Both ratings make our overall product practical for outdoor use and eliminates possible dust or water damage from field work. Finally, for simplicity, the enclosure consists of only one charging port and a switch, which are both very intuitive components and can be used with ease.
Questions? Come say Hello!
The team is available from 10:00 am to 12:30 pm on April 13th, 2021.
Meet Team Level-Up

Kathryn Sarmiento
Project Manager/Software Support
4th year Electrical Engineering student at the University of Calgary. Completed a 16-month internship with ATCO Gas & Pipelines as an Integrity Engineering Co-op Student. Technical interests include software design and implementation, quality assurance, and expanding knowledge on control engineering. Some hobbies include sketching and painting.
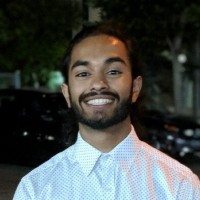
Nakul Sawant
Software Lead
4th year Electrical Engineering student at the University of Calgary, who is passionate about machines and robotics. Enjoys tinkering around with anything that has to do with this topic, especially integrating robotics with IOT (Internet of Things). Working in robotics would be a career goal.
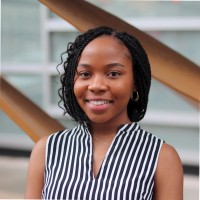
Veronica Azichoba
Hardware Lead
4th year Electrical Engineering student at the University of Calgary. Completed a 16-month internship at TC Energy as a Pipe Integrity Project Execution Intern. Technical interests include data organization, analysis, project design and drawings for project implementation. Hobbies include art & design, interior décor, or any aspect where creativity can be showcased.
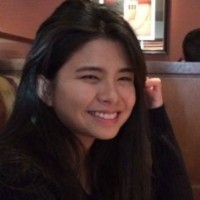
Pauline Abalos
Test Lead/Hardware Support
4th year Electrical Engineering student at the University of Calgary. Completed a 12-month internship in Toronto at Hydro One as a Project Estimating Intern. Technical/business interests include power systems, electric power transmission, photovoltaics, and project management.
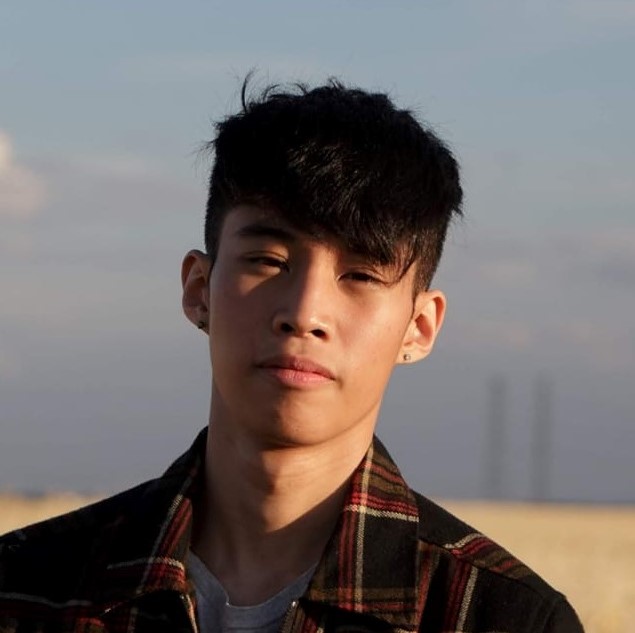
Gavin Gavieres
Mechanical Lead
4th year Electrical Engineering student at the University of Calgary. Completed a 12-month internship with the Canadian Pacific Railway, as part of their crossing compliance team. Technical interests include learning about renewable energy technologies and quality of life advancements.
Partners and Mentors
Team “Level-Up” would like to say a huge thank you to the following people who have in their own way supported us for the entirety of this capstone project.
To George Dalekos and Approach Controls Inc., for sponsoring our project and supporting us. To Kirsten Sarmiento for being our industry mentor and providing the team with her support and feedback. To Dr. Mohamed Helaoui, our academic advisor, who provided the team with technical and professional knowledge. To Mateo Alzate, our technical advisor, for always supporting the team with technical questions and helping us come up with efficient solutions. To our TA, Aakash Bhatt for his continuous support and guidance throughout this project. Last but not least, to Wilson Abalos for all his help with the hardware portion of the project and providing us with his technical expertise.
It is indeed safe to say that each member of our team has learnt a great deal from this opportunity and for that we say THANK YOU!