Project Category: Multidisciplinary
Join our presentation
About our project
Every year, for the annual Baja SAE student design competition, Schulich Off-Road designs and builds a new vehicle. The vehicle’s frame is a welded chassis made of steel tubes. Hundreds of hours each year are spent on profiling chromoly tubes by hand so that they mate together properly for welding; the tube ends must interface with the contours of the other tubes with a very tight tolerance so that they can be welded together. This process, called ‘coping’, requires a 0.050” tolerance which takes considerable skill and practice to do by hand. The chassis is composed of about 60 tubes, and each tube has two ends to be profiled. It currently takes at least 250 hours of labour to cope all tubes by hand. To solve these labour and cost challenges, we designed an automated plasma cutter to accurately manufacture coped tubes. Our project uses two axes of motion, which allows the plasma cutter head to move to any point on the tube: (i) the tube rotates in a chuck (ii) the plasma cutter slides up and down the tube. This allows any tube end profile to be cut.

Meet our team members




Details about our design
HOW OUR DESIGN ADDRESSES PRACTICAL ISSUES
The main issues with shaping the profiles by hand is the accuracy and the time. Automating the process solves both issues of time and accuracy by removing human error. Another issue that arose was the time it would take to switch workpieces. This was solved by using a 3D printed clamp to hold on to the material. The clamp design uses two wing nuts to cause enough force to hold the workpiece. By loosening the wing nuts the workpiece can be removed and another workpiece can replace it. The clamp design also aligns the workpiece without causing damage.
WHAT MAKES OUR DESIGN INNOVATIVE
FAST | The CNC Tube Notcher can accurately cut custom end profiles of chromoly tubes in >10s with minimal setup time. With the help of the custom SOLIDWORKS macro, SheetCams and Mach 4 a CAD model of a tube is converted into a G-code allowing the plasma cutter to cut the tube precisely. |
PORTABLE | Our design offers a portable solution to DIY hobbyists and small manufacturing facilities without compromising in quality. |
MODULAR | With all components bolted on to a single chassis, our design can easily be disassembled and upgraded to suit custom manufacturing needs. |
CHEAP | Coming under $5000 the CNC Tube Notcher is in a class of its own compared to the automated tube coping and cutting machines available on the market. |
SCRIBER | In addition to cutting tubes, the CNC Tube Notcher can also mark the bend locations on tubes that need to be bent after they have been cut. |
WHAT MAKES OUR DESIGN SOLUTION EFFECTIVE
It currently takes at least 250 hours to shape the profiles by hand. Our design allows for one person to shape the profiles accurately and only take around 10 seconds per cut. If we assume tooling takes about 30 seconds then it would take 40 minutes to turn raw material into ready to weld tubes. This is a reduction of 375% in manufacturing time.
With a tolerance of 0.050”, our design solution significantly increases the accuracy and reduces the errors caused by hand tools and manual manufacturing methods. With multiple tubes welded on the same frame, these errors would add up resulting in weaker parts and premature failure. With the help of or our automated solution these errors can be eliminated.
HOW WE VALIDATED OUR DESIGN SOLUTION
- Costing under $5,000
- Locating cuts within a ±0.050 inch tolerance
- Cutting material as thick as 0.125 inch and tubes as long as 20 feet
- Setting up and performing cuts in under 60 seconds
- Meeting CSA Z-432-16 criteria for safe, manned, rotating machinery
- Resisting a 50-Newton load without compromising cut quality.
FEASIBILITY OF OUR DESIGN SOLUTION
- Welded, single-structure chassis encourages modularity
- 3D-printed torch adapter and can interface with a wide variety of plasma cutters
- Can interpret various common file types, including DXF, SLDPRT, and raw G-code.
- Compatible with most CAD programs
- Accepts common CNC machine cables.
Partners and mentors
Thank you to our course instructor Dr. Roes (Arief) Budiman, our academic advisor Jeff Pieper and Schulich Off-Road For sponsoring our project.

Our photo gallery
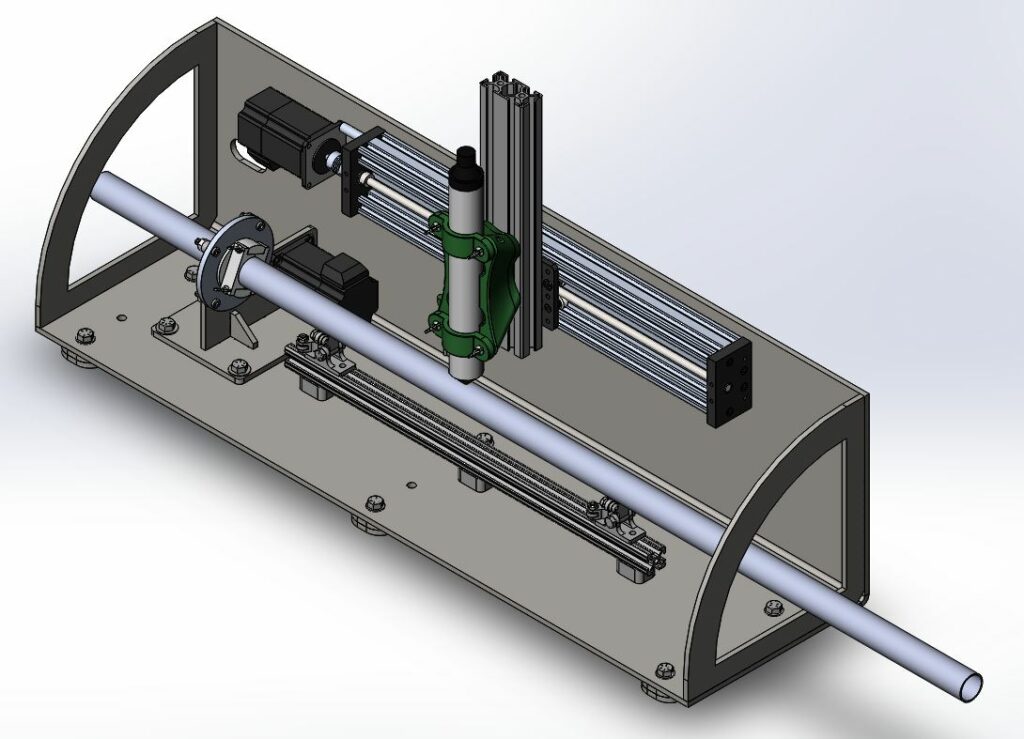
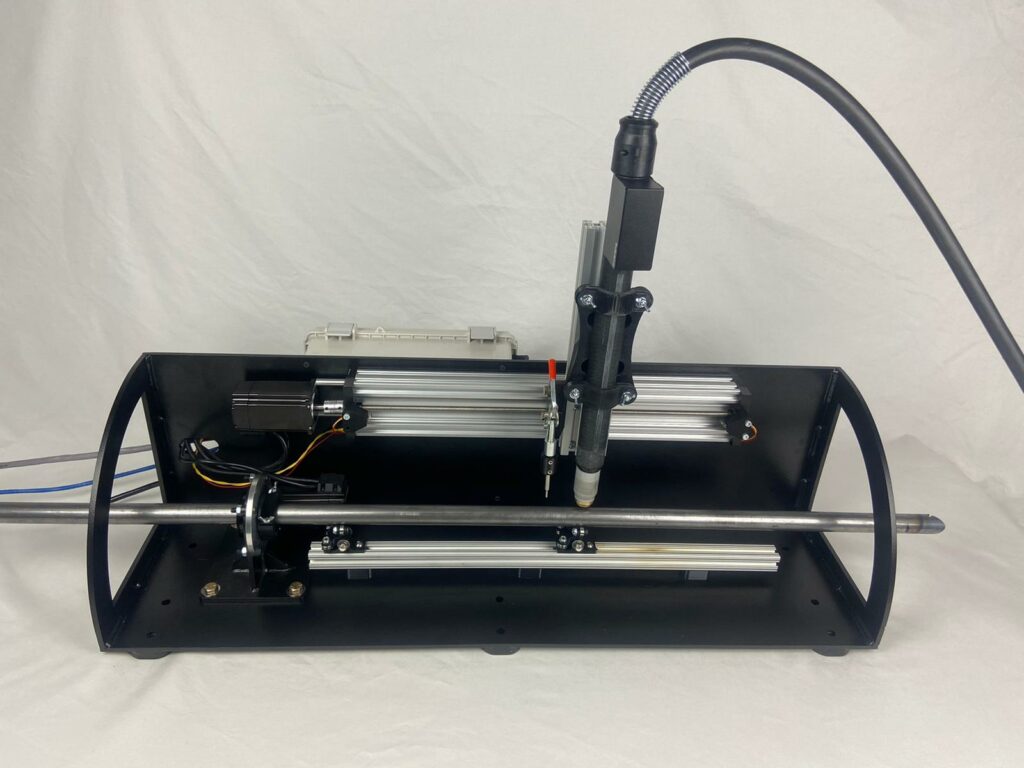

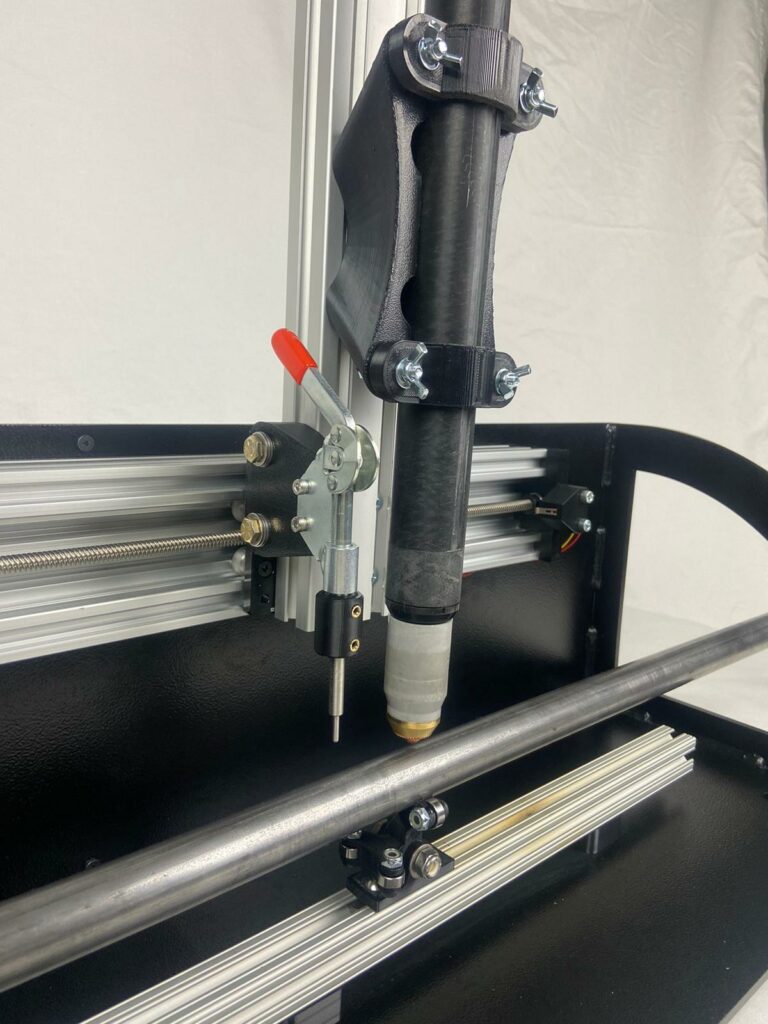
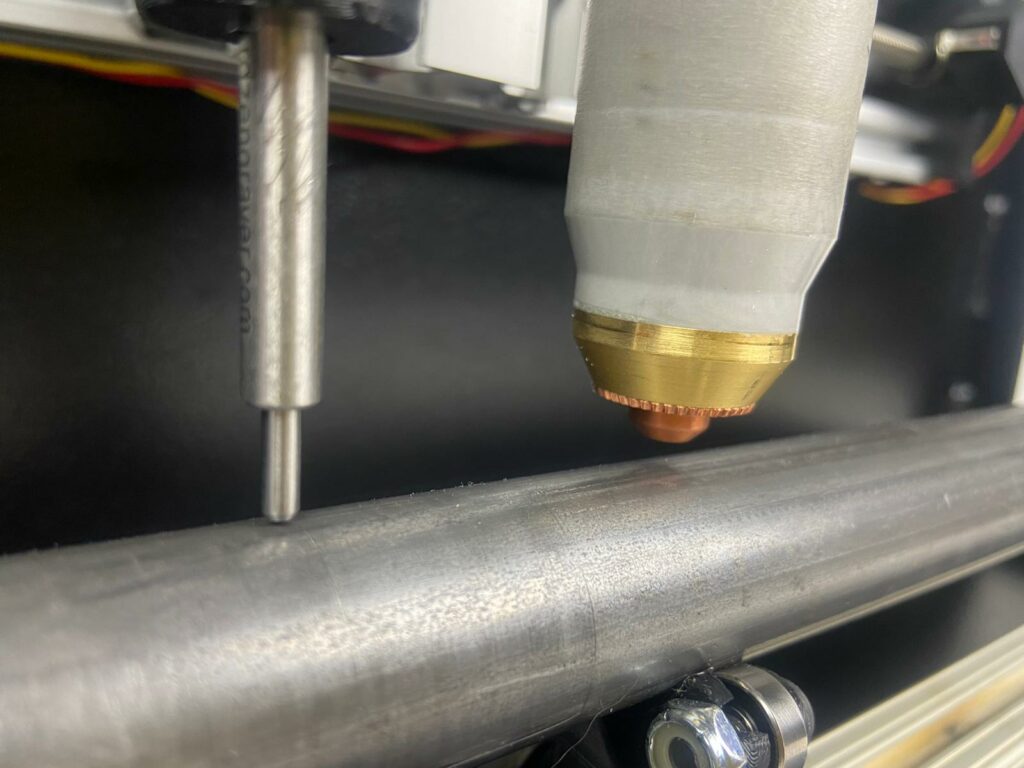
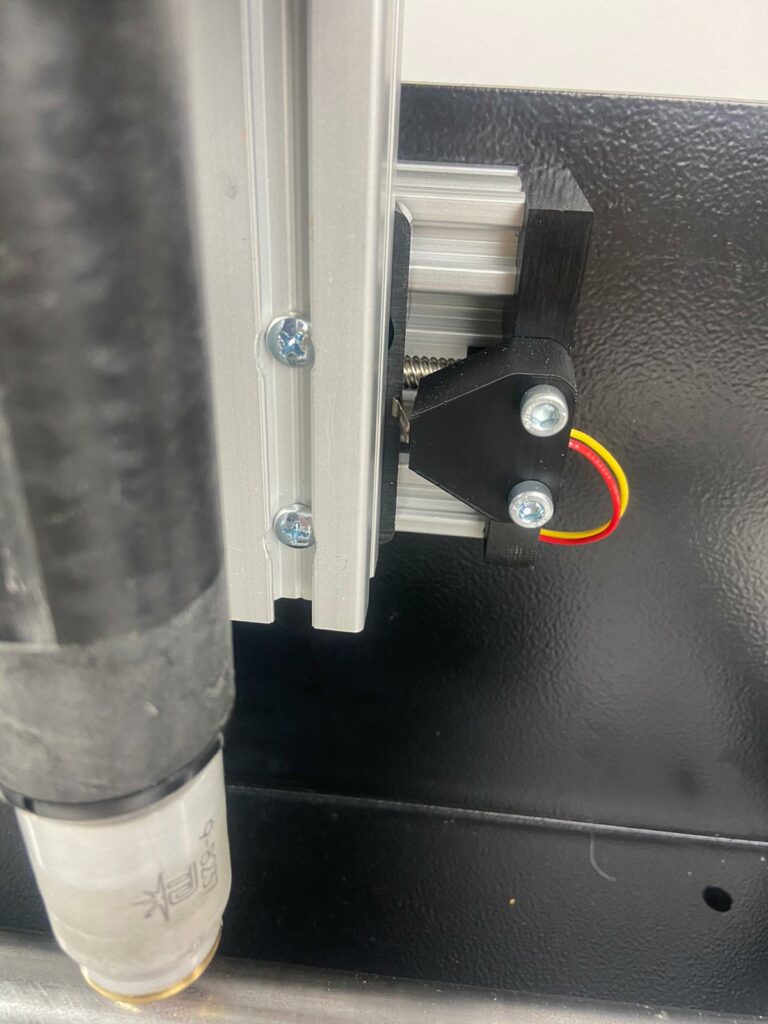
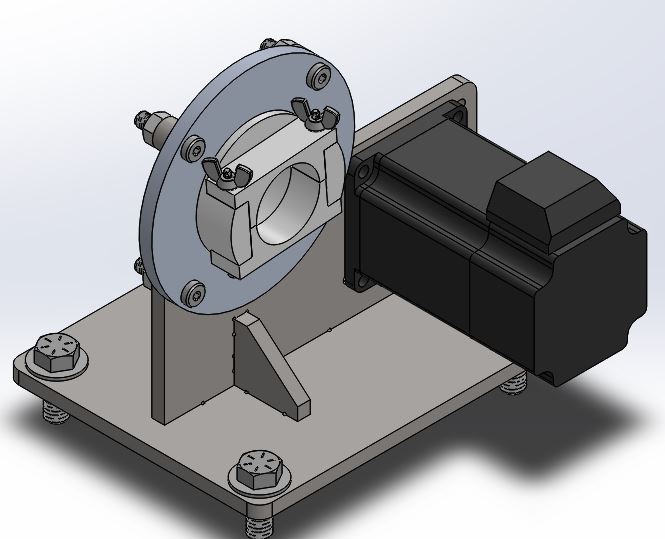
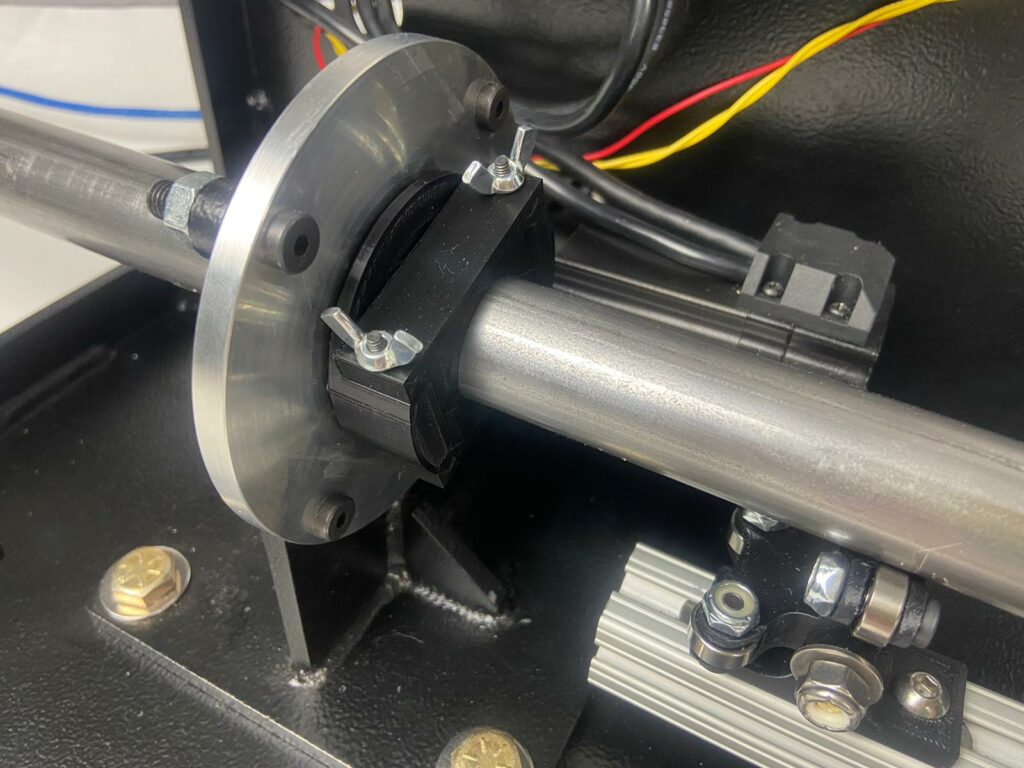
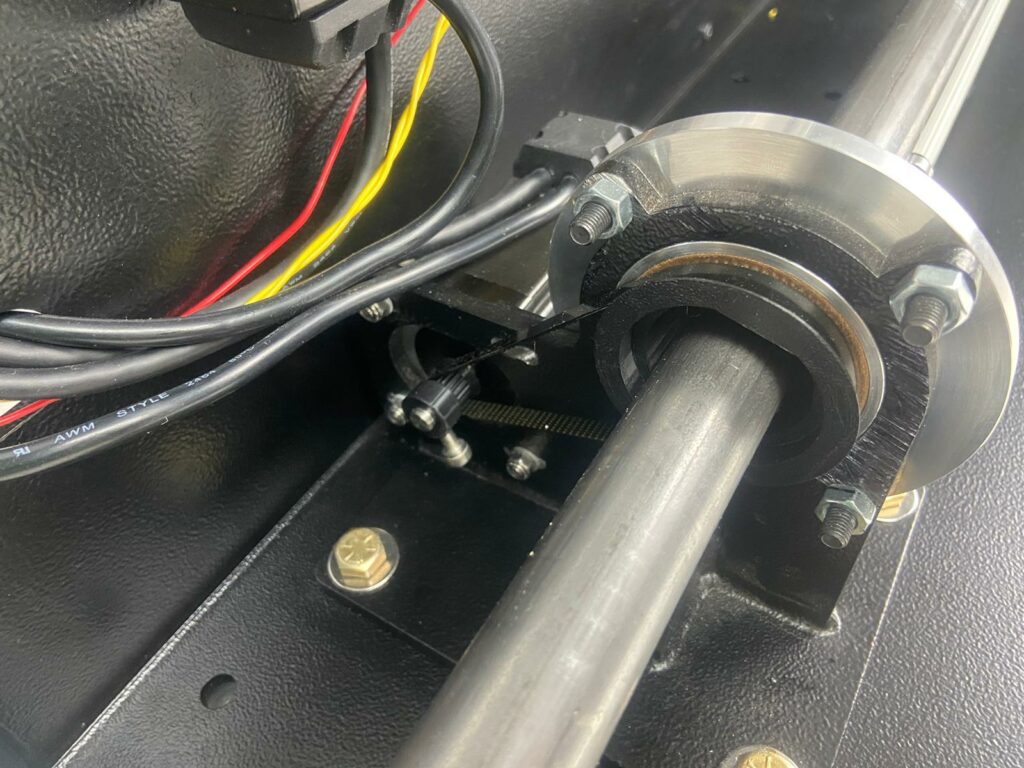
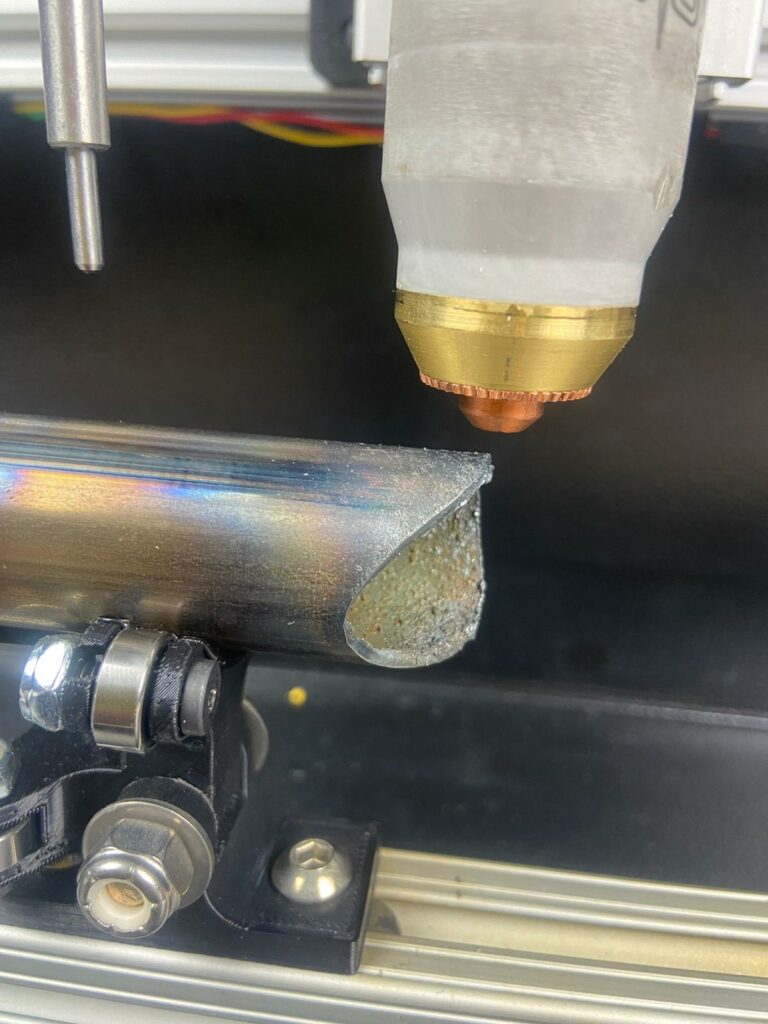
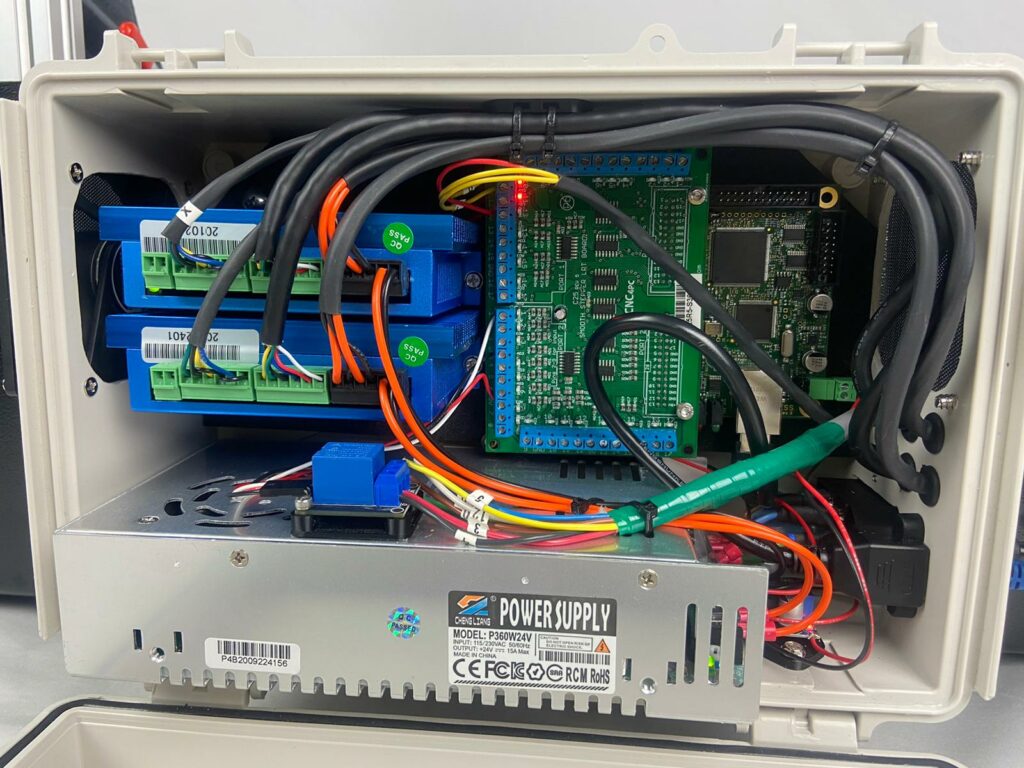
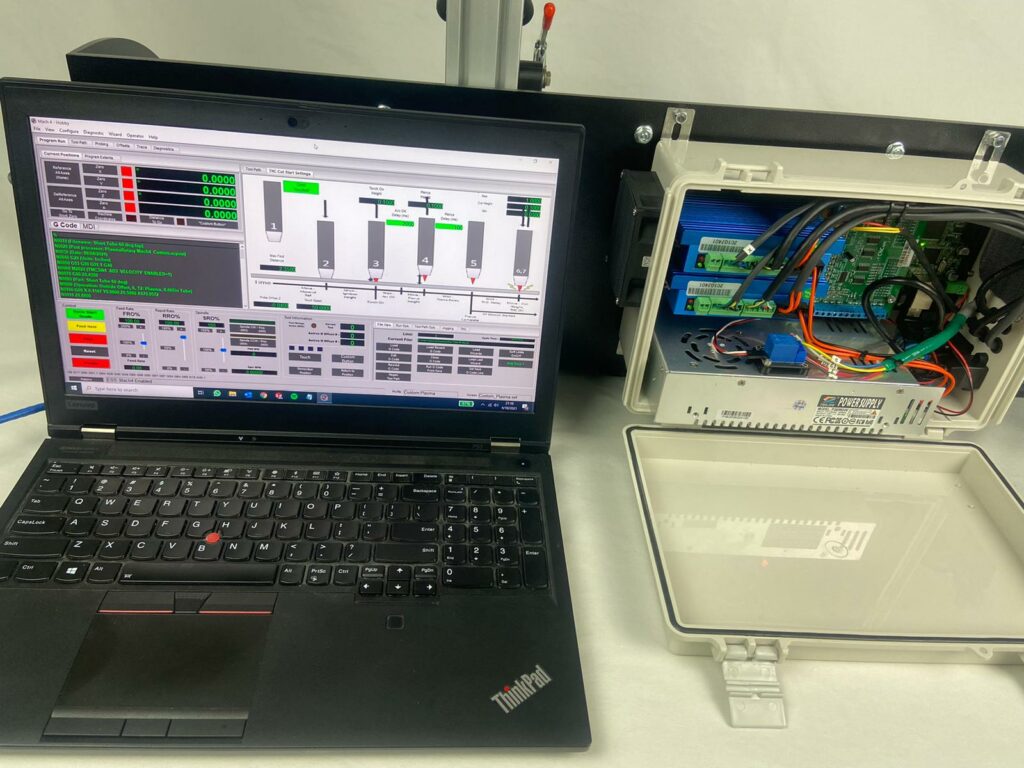
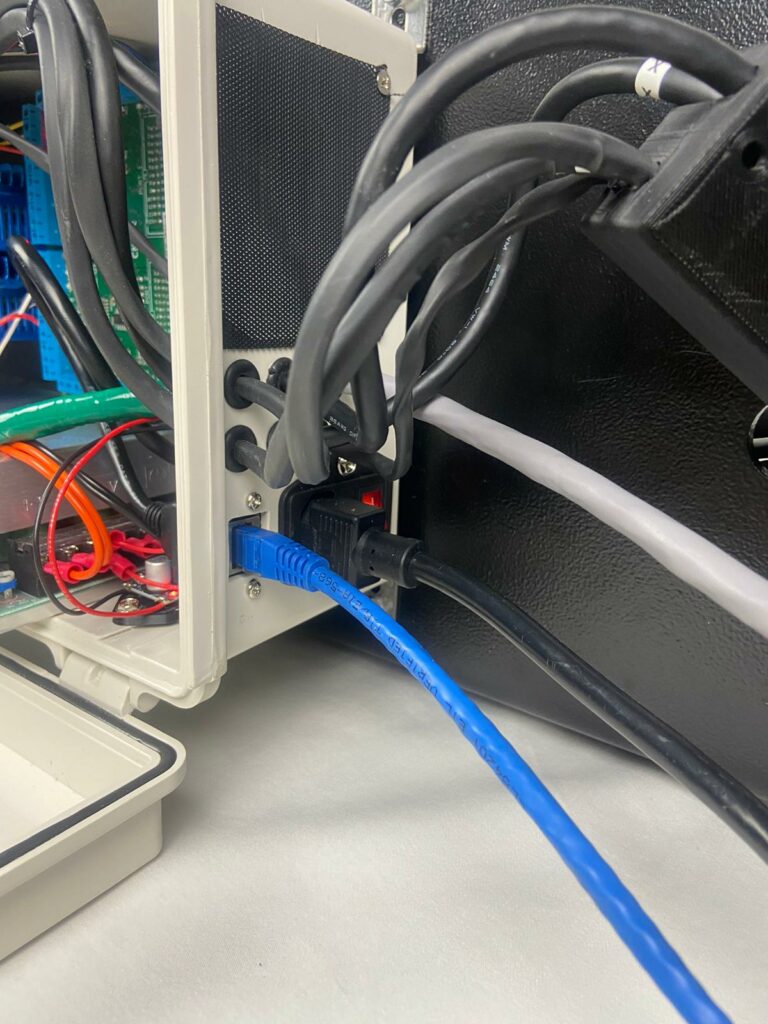
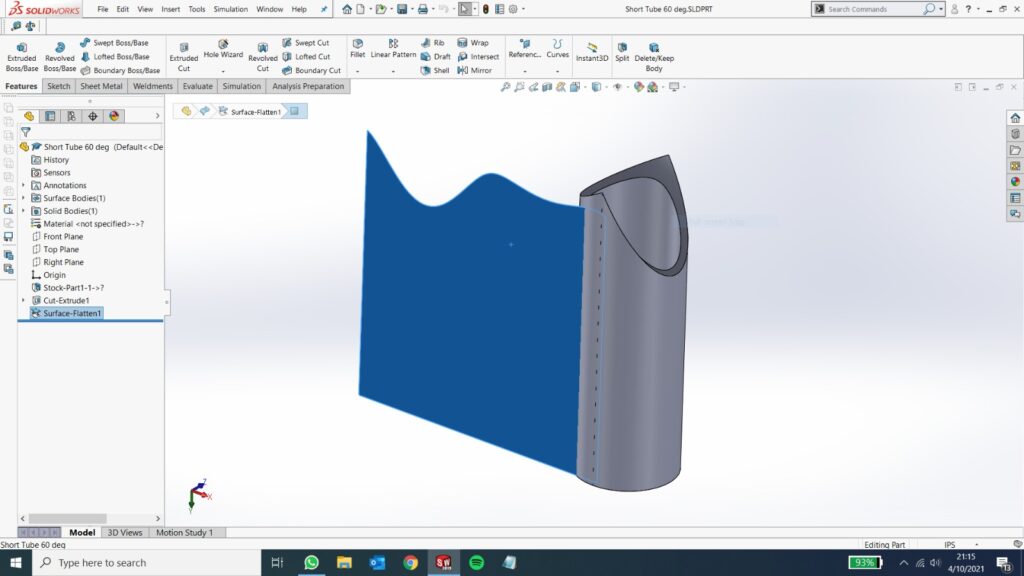
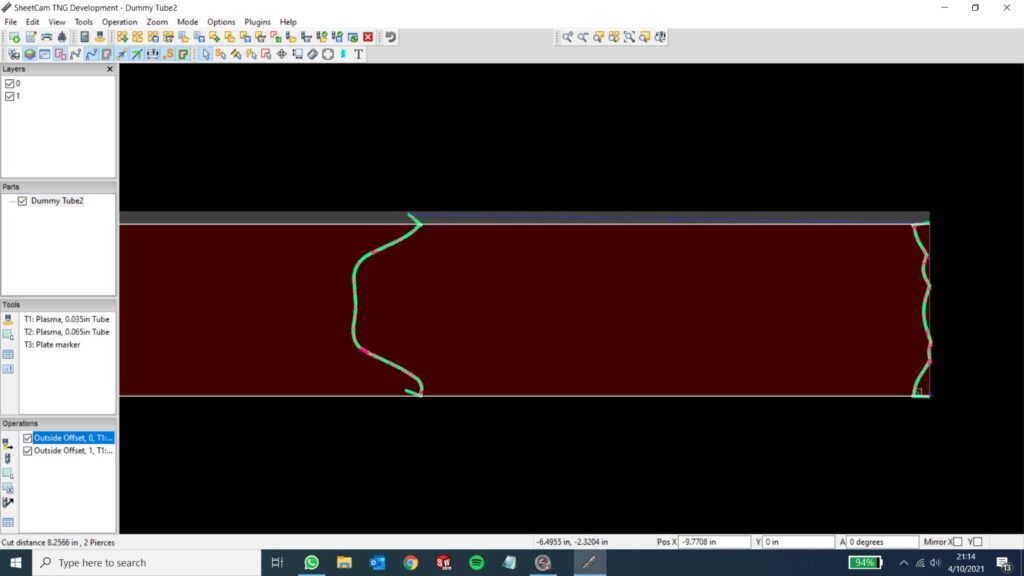
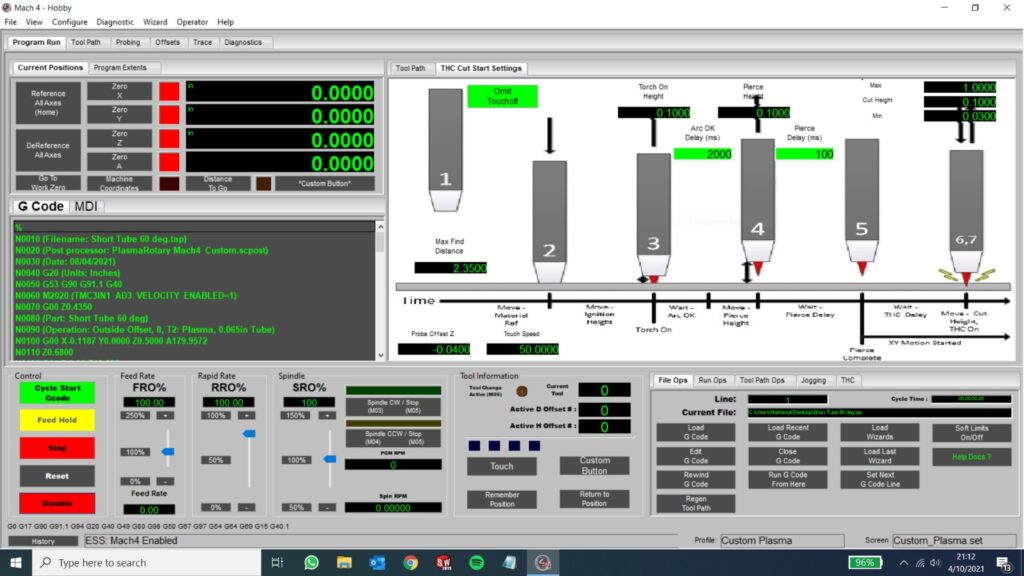
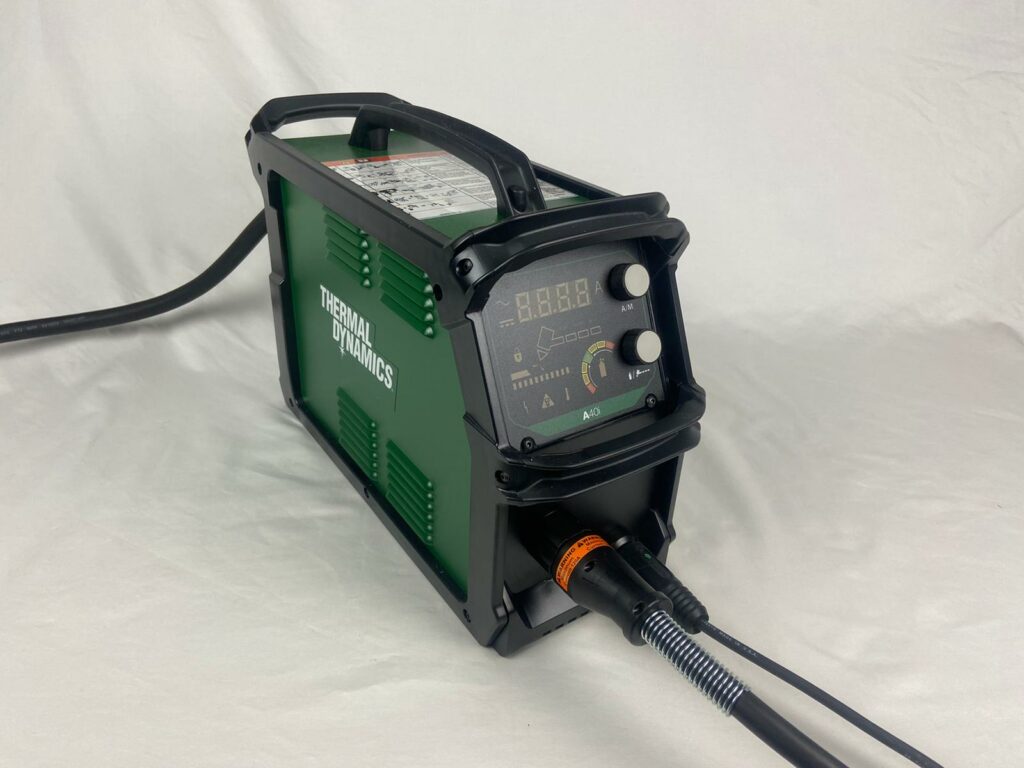